Hemming die and hemming system for the automotive industry
Company Development
- In 2011, TTM was founded in ShenZhen.
- In 2012, Moving to DongGuan; Building cooperation relationship with Magna International Inc.
- In 2013 Introducing more advanced equipments.
- In 2016, Introduced large-scale CMM equipment and 5 axis CNC equipment; Cooperated with OEM Ford Completed Porsche, Lamborghini and Tesla CF projects.
- In 2017, Moving to current plant location; CNC was increased from 8 to 17 sets. Top Talent Automotive Fixtures & Jigs Co.Ltd was established
- In 2018, Cooperated with LEVDEO automotive and completed the automotion production line. 4-axis high-speed CNC was introduced, the total Qty of CNC reached 21.
- In 2019, Dongguan Hong Xing Tool & Die Manufacturer Co.,Ltd was established. (One stop service) Cooperated with Tesla Shanghai and Sodecia Germany. Built a new R&D laboratory for automation.
- In 2020, Cooperated with OEM ISUZU in SA ;Completed the RG06 One-Stop Service.
- In 2021, Moving forward with the quality belief to create a world-class enterprise.
- In 2022, TTM Group office was founded in Dongguan City, New CNC 4 axis*5 sets, New Press*630 tons, Hexagon Absolute Arm.
- In 2023, TTM is building a new plant for checking fixture&welding fixture business; adding one 2000T press.
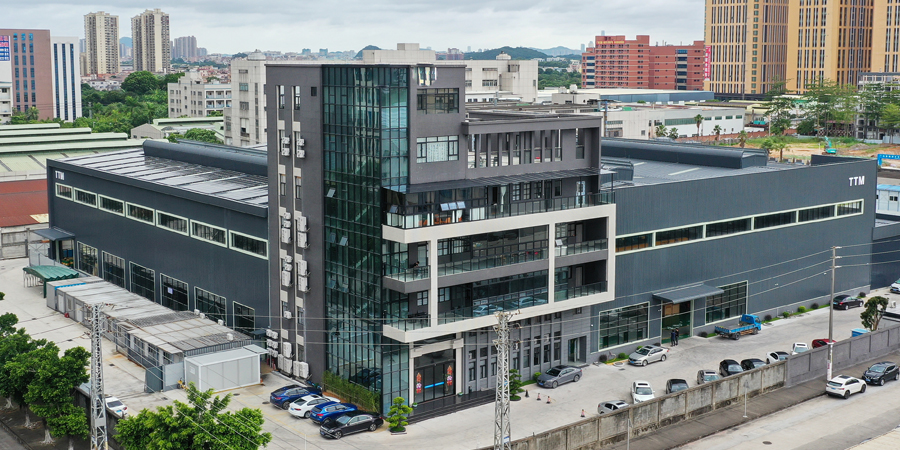
Checking Fixture & Welding Fixture Factory (Total area: 9000m² )
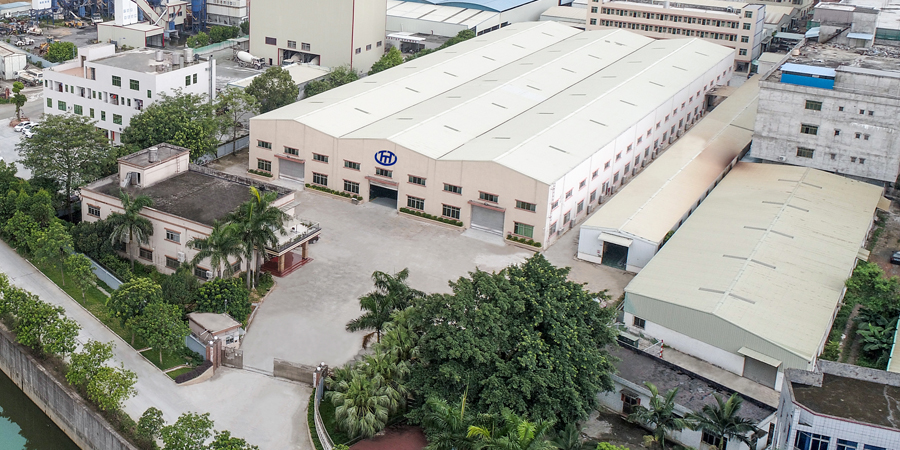
Stamping Tools & Dies and Machined Parts Factory (Total area: 16000m²)
Products Description
Product Name | Hemming dies |
Application | Automotive hoods, doors, tailgates etc. |
Type | Hemming die system |
Pneumatic Component Brand | SMC, FESTO, TUENKERS, CKD, Manual clamp |
Electrical Component Brand | OMRON, Mitsubishi, Siemens, Balluff |
Material(Block, Locating Pin) | 45# Steel, Copper, Stainless Steel |
Controlling Way | Air Control(Pneumatic Control Valve), Electrical Control(Solenoid Valve ), Manual, No solenoid valve required Provide connector switch |
Clamping Way | Pneumatic, Manual |
Communication Way | EtherCAT, PROFINET, CC-LINK |
Communication Relay Box | Electric box wiring way, Quick socket type, Solenoid valve island type |
Piping Way | Single layer tube, Flame retardant tube, Copper/Stainless Steel Tube |
Surface Treatment | Painting, Painting+Black Oxidization, Zinc-Coated, Powder Painting |
Lead Time | 2-4 Weeks for design and design review; |
10-12 weeks for manufacturing after design approval | |
7-10 Working days for air shipping; | |
4-5 Weeks for ocean sipping | |
Die Life | Depends on customer’s production capacity |
Quality Insurance | CMM Inspection |
Test with Samples | |
Onsite Buy-Off | |
Online video Web Conference Buy-Off | |
Buy-Off Problems Solving | |
Package | Wooden Boxes for samples;Wooden Boxes or Pallets for fixtures; |
What is the automotive hemming die?
An automotive hemming die is a specialized tool used in the manufacturing process to shape and secure the edges of sheet metal components that form the body of a vehicle. Hemming is a technique commonly employed in the automotive industry to join two pieces of sheet metal by folding the edge of one sheet over the other, creating a clean and often reinforced seam.
The primary purpose of an automotive hemming die is to achieve precise and consistent folds in the sheet metal, ensuring that the edges are securely joined together. This process is crucial for manufacturing various components of a vehicle, including doors, hoods, fenders, and other body panels. The quality of hemming directly influences the structural integrity, appearance, and durability of the final automotive product.
Here are some key aspects and functions of an automotive hemming die:
Shaping Edges: The die is designed to shape and fold the edges of sheet metal to create a seamless and finished appearance. This is especially important in the automotive industry, where aesthetics and aerodynamics are significant factors.
Reinforcement: Hemming not only provides a clean look but also reinforces the joined edges, enhancing the strength and rigidity of the assembled components. This is crucial for maintaining the structural integrity of the vehicle.
Versatility: Automotive hemming dies are designed to accommodate various sheet metal thicknesses and compositions, providing versatility in the manufacturing process. This adaptability ensures that the tool can be used for different types of vehicle models and designs.
Efficiency: The use of hemming dies streamlines the manufacturing process by automating the folding and joining of sheet metal edges. This leads to increased efficiency in production, reduced manual labour, and improved overall output.
Consistency: Achieving consistent and high-quality results is a key advantage of using hemming dies. Automation ensures that each component is produced with precision, reducing the likelihood of defects and variations in the final product.
Innovation: Advancements in hemming die technology often incorporate features such as adaptive control systems, artificial intelligence, and modular designs. These innovations contribute to improved control over the hemming process and allow for easier integration into modern manufacturing setups.
The development of advanced hemming dies, like the hypothetical PrecisionHem 2024 mentioned in the previous response, showcases the ongoing efforts in the industry to enhance the efficiency, sustainability, and overall quality of automotive manufacturing processes. Hemming dies play a crucial role in achieving the desired standards for modern vehicles, meeting both functional and aesthetic requirements.
Solutions(Turnkey Solutions Service)
Body In White Assembly Systems:
1, Hemming die
2, Complete Car Body Welding Line
3, Single Stand-alone Welding Cell
CCB ASSY Welding Fixture, Floor Pan ASSY Welding Fixture, Wheelhouse ASSY Welding Fixture, AB Ring ASSY AB Welding Fixture, Seat ASSY Welding Fixture, Front Seat Cross Member Welding Fixture, Front End ASSY Welding Fixture, Dash Panel ASSY Welding Fixture, Cowl ASSY Welding Fixture and Rocker ASSY Welding Fixture manufacturer, design company and factory.
ISO Management System For Hemming Die
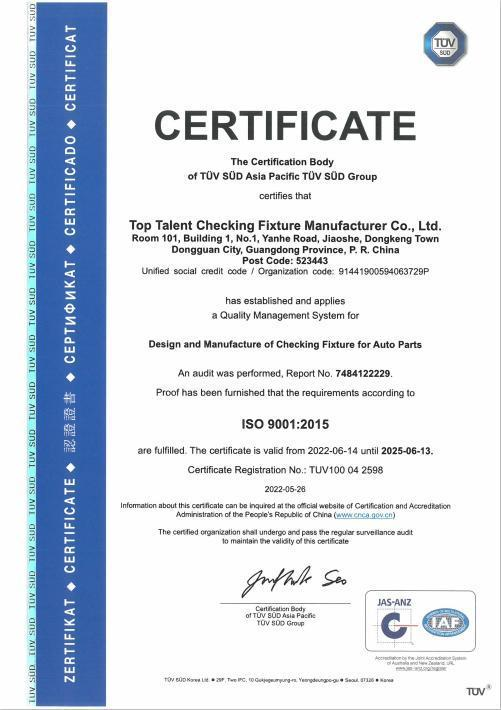
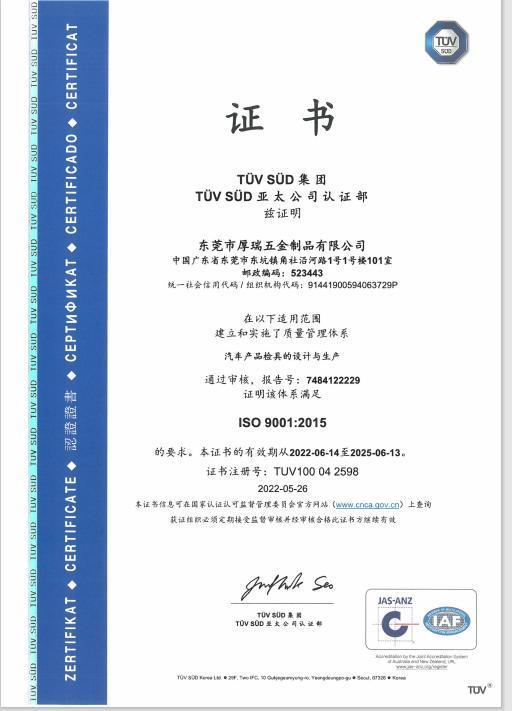
Our Hemming Die Team
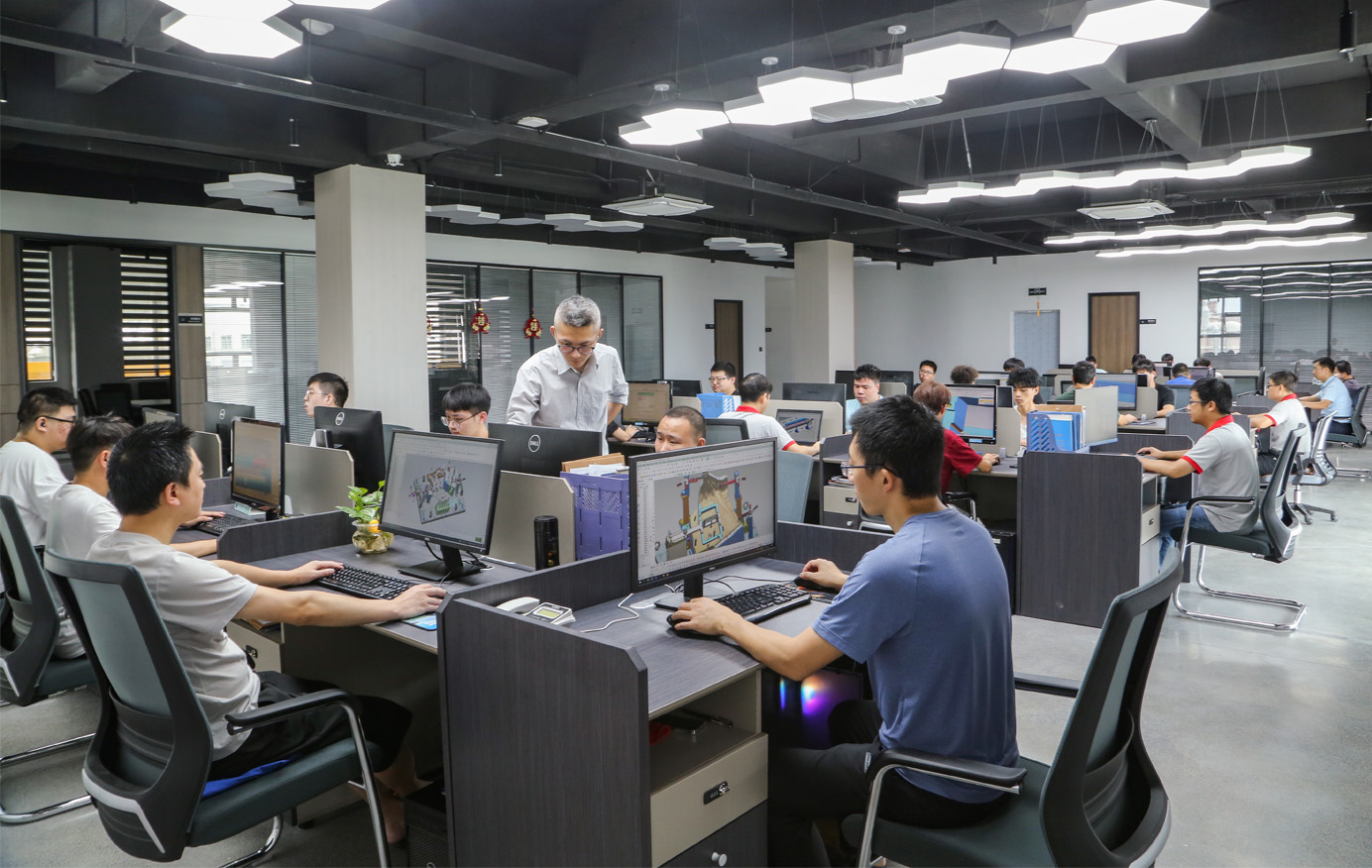
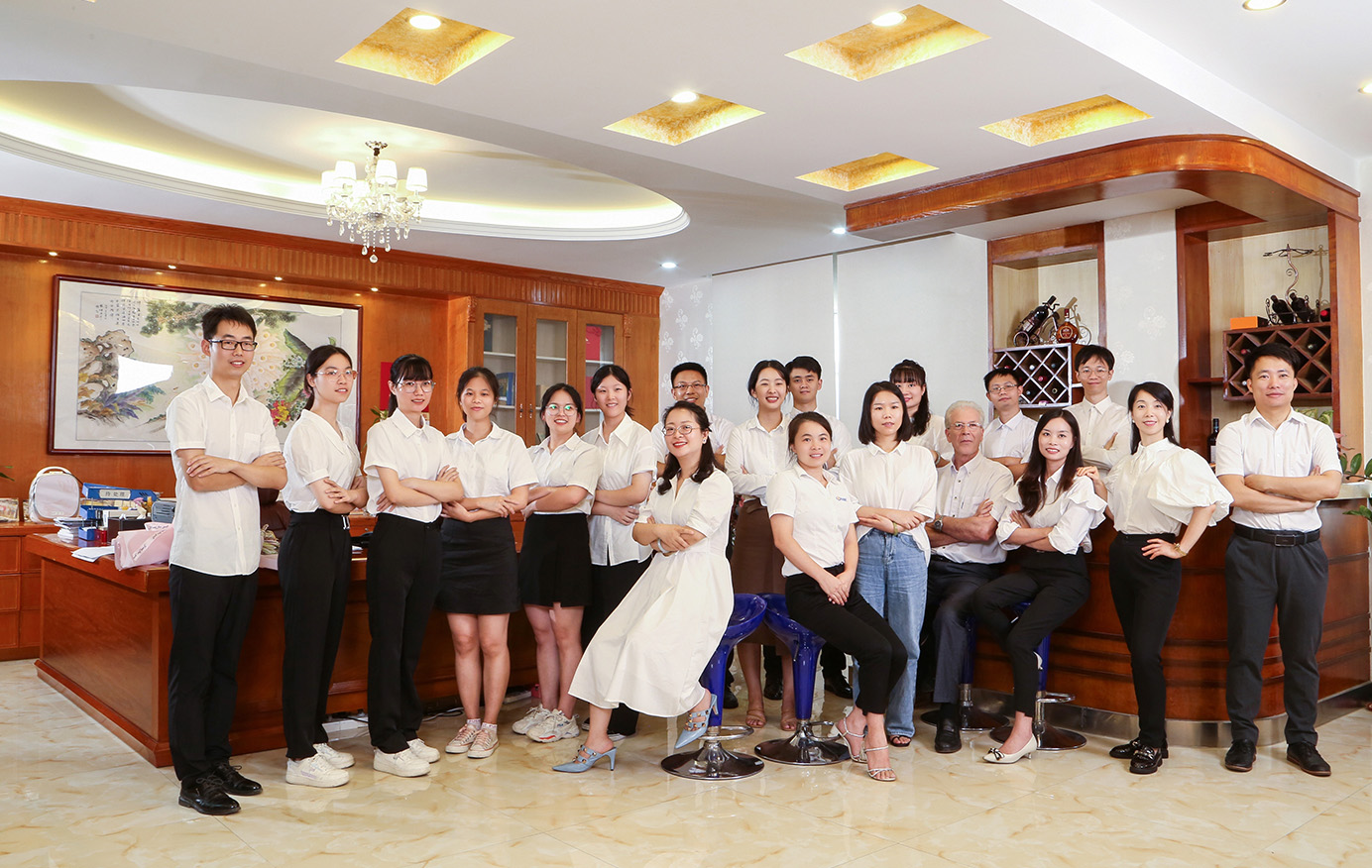
Our Advantages
1.Rich experience in automatic manufacturing and enterprise management.
2.One Stop Service for stamping tool, checking fixture, welding fixtures and cells to achieve timing and cost saving, communication convenience, to maximize customer profits.
3.Professional engineering team to finalize the GD&T between single part and assembly component.
4.Turnkey Solution Service-Stamping Tool, Checking Fixture, Welding Fixtures and Cells with one team.
5.Strong capability with international technical support and partnership cooperation.
6.Big capacity: Checking Fixture, 1500 sets/year;Welding Fixture and Cells, 400-600 sets/year; Stamping Tools, 200-300 sets/year.
We have more than 352 employees, 80% of which are senior technical engineers. Tooling division: 130 employees, Welding fixture division:60 employees, Checking fixture division:162 employees, We have a professional sales & project management team, long-term service overseas projects, from RFQ to production, shipment, after-sales, our team can handle all problems for our customers in Chinese, English and German Language.
Major Projects Experience Of Welding Cells And Welding Fixtures
Major Welding Fixtures Project(2019-2021) | |||||
Item | Description | Type | Project Name | Qty(Sets) | Year |
1 | CCB WF | Arc Welding | VW MEB31 | 60 | 2019-2021 |
2 | CCB WF | Arc Welding | VW MEB41 | 10 | 2020 |
3 | CCB WF | Arc Welding | VW 316 | 4 | 2020 |
4 | CCB WF | Arc Welding | Ford T6 | 8 | 2021 |
5 | CCB WF | Arc Welding | ISUZU RG06 | 3 | 2020 |
6 | CCB WF | Arc Welding | Bcar,BSUV | 6 | 2020 |
7 | CCB WF | Arc Welding | Bcar,BCAR | 7 | 2020 |
8 | Floor Pan WF | Sopt Welding | SK326/0RU_K Karoq RU | 15 | 2019 |
VW316/5RU_K Tarek RU (19003) | |||||
9 | WS Spring Link WF | Arc Welding | WL/WS | 4 | 2019 |
10 | Crossmember Brackets WF | Arc Welding | WL/WS | 12 | 2019-2021 |
11 | Front Bumper WF | Arc Welding | VW281 | 14 | 2019 |
12 | Chassis WF | Arc Welding | ISUSU RG06 | 18 | 2019 |
13 | SL ASY and MBR and EXT ASY | Spot and Arc Welding | Ford P703 | 25 | 2019-2021 |
14 | CCB WF and Wroking Cell | Arc Welding | ISUSU RG06 | 6 | 2020 |
15 | Front Seat Cross Member WF | Sopt Welding | Volkswagen AG MEB316(20001) | 4 | 2020 |
16 | Floor Pan WF and Grippers | Sopt Welding | AUDI/ PORSCHE PPE 41(19017 Phase 1) | 18 | 2020 |
17 | Wheel House WF and Grippers | Arc Welding | Ford BX755(19018) | 6 | 2020 |
18 | AB Ring WF and Grippers | Arc Welding | Ford BX755(19018) | 14 | 2020 |
19 | Dash Panel WF and Grippers | Sopt Welding | South Africa Ford T6(17028-1) | 10 | 2020 |
20 | Cowl WF and Grippers | Spot Welding | South Africa Ford T6(17028-3) | 6 | 2020 |
21 | Front End WF and Grippers | Spot and Arc Welding | South Africa Ford T6(17025) | 10 | 2020 |
22 | Rocker WF and Grippers | Spot Welding | South Africa Ford T6(19029) | 8 | 2020 |
23 | Floor Pan WF and Grippers | Sopt Welding | AUDI/ PORSCHE PPE 41(19017 Phase 2) | 63 | 2021 |
24 | Rear Bumper and Chassis WF | Arc Welding | Ford P703&J73 | 36 | 2020-2021 |
Major Welding Fixtures Project(2022) | |||||
Item | Description | Type | Project Name | Qty(Sets) | Year |
25 | Middle Channel Reinforcement WF | Sopt Welding | Vinfast VF36 | 8 | 2022 |
26 | Floor Pan WF and Grippers | Sopt Welding | AUDI/ PORSCHE PPE 41(19017 Phase 3&4) | 39 | 2022 |
27 | Floor Pan WF | Sopt Welding and Projection Welding | Ford P703 PHEV | 29 | 2022 |
28 | Floor Pan WF and Grippers | Sopt Welding | Porsche E4 Floor Pan(21050) | 16 | 2022 |
29 | Floor Tunnel WF | Laser marking | VW Floor Tunnel(21008 ) | 2 | 2022 |
30 | Seat ASSY WF and Tooling | Arc Welding | BYD Seat ASSY | 40 | 2022 |
31 | Floor Pan WF | Spot and Arc Welding | Ford Refurbishment | 24 | 2022 |
32 | CCB WF | Arc Welding | VW Cyclone CCB(21037) | 10 | 2022 |
33 | CCB WF | Arc Welding | VW MQB37(22022) | 16 | 2022 |
34 | A&B-Pillar WF | Spot Welding | Gestamp GS2203 | 8 | 2022 |
35 | Robot Cell Base | NA | VW Cyclone | 4 | 2022 |
Hemming Dies Manufacturing Center
We can build all kinds of different size welding fixture including large size as we have big CNC Machines. With a variety of mechanical equipment such as milling, grinding, wire cutting machines and drilling machines, we can effectively and accurately control the processing process.
25 sets of CNC with 2 shift running
1 Set of 3-Axis CNC 3000*2000*1500
1 Set of 3-Axis CNC 3000*2300*900
1 Set of 3-Axis CNC 4000*2400*900
1 Set of 3-Axis CNC 4000*2400*1000
1 Set of 3-Axis CNC 6000*3000*1200
4 Set of 3-Axis CNC 800*500*530
9 Set of 3-Axis CNC 900*600*600
5 Set of 3-Axis CNC 1100*800*500
1 Set of 3-Axis CNC 1300*700*650
1 Set of 3-Axis CNC 2500*1100*800
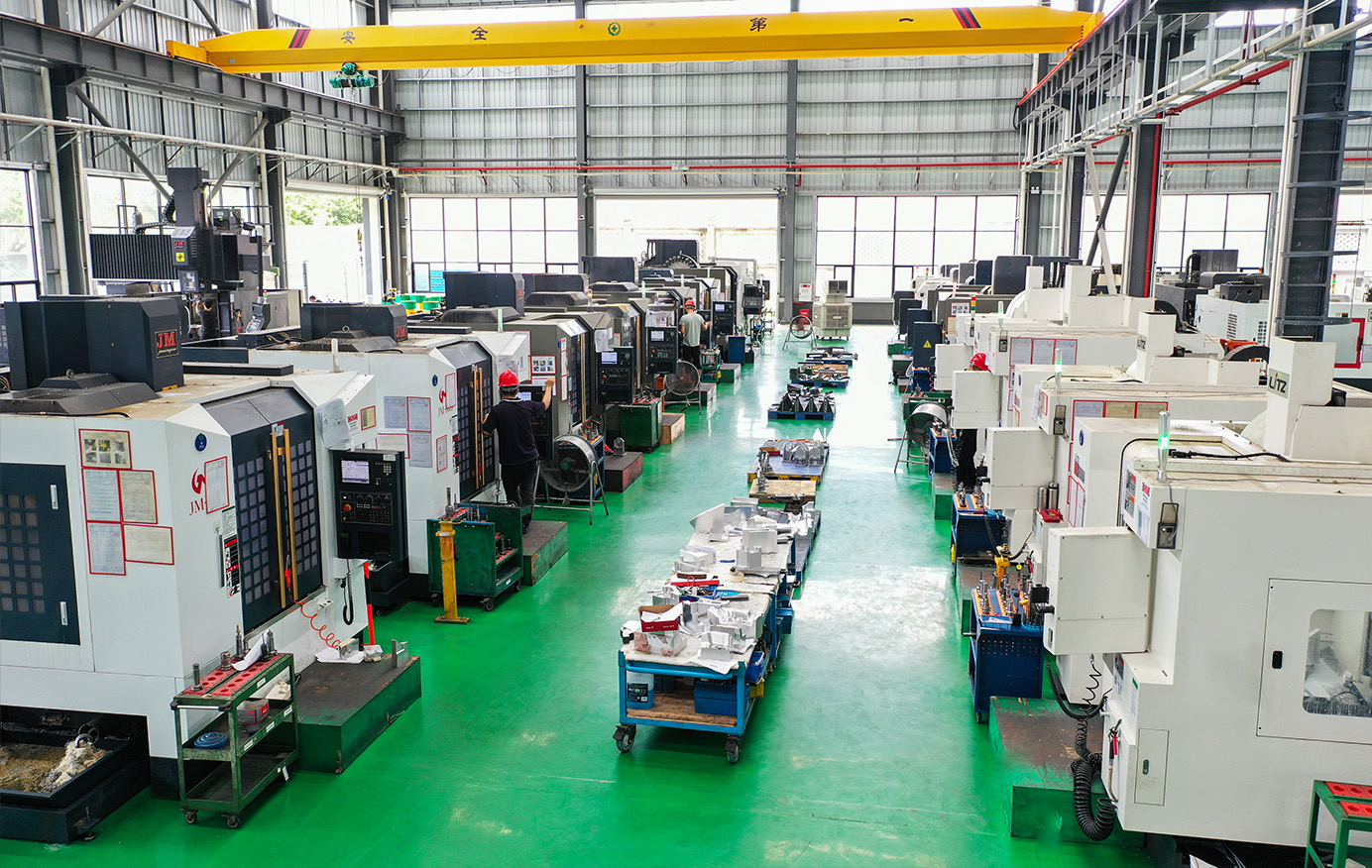
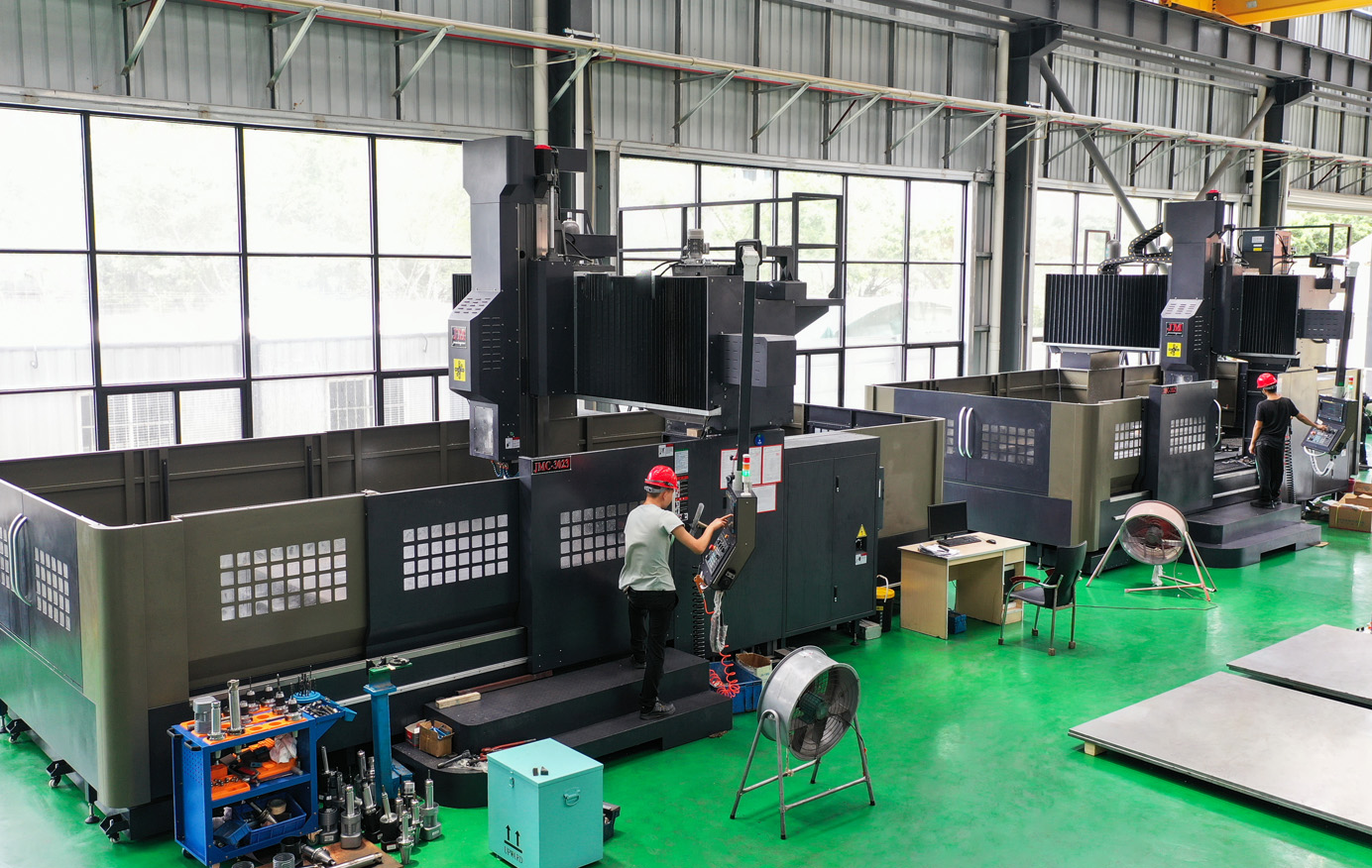
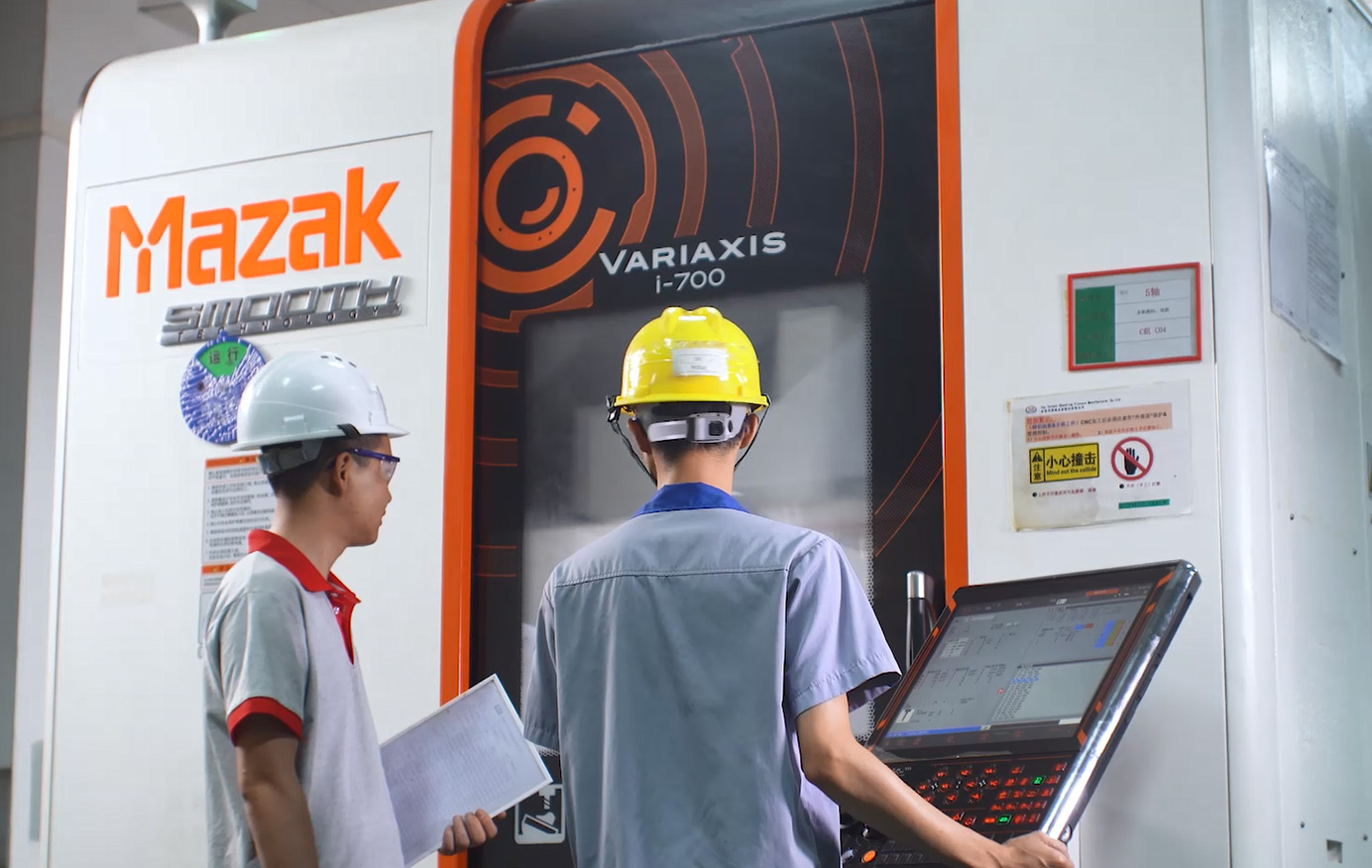
5 Axis CNC -Machine
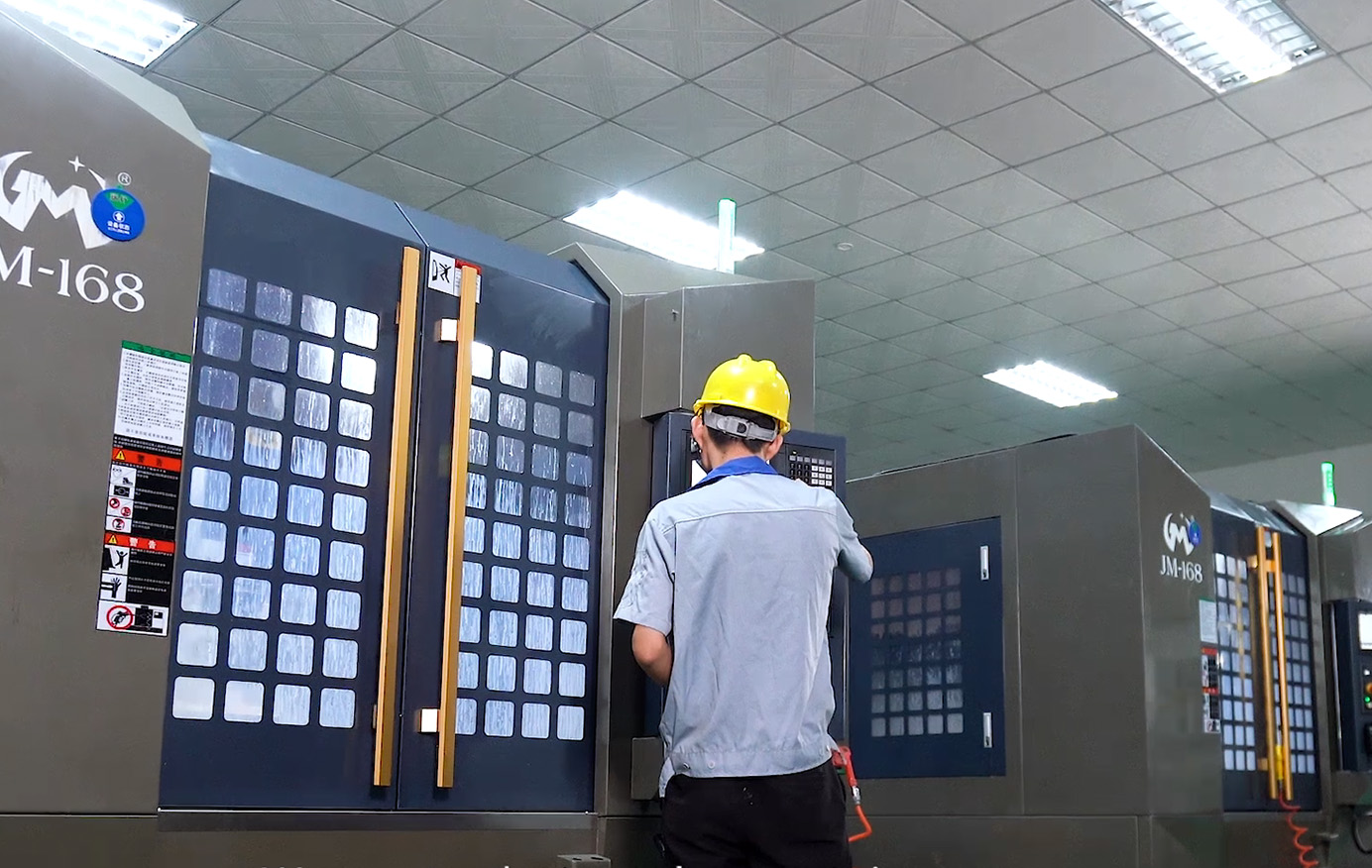
4 Axis CNC -Machine
Hemming Die Assembly Center
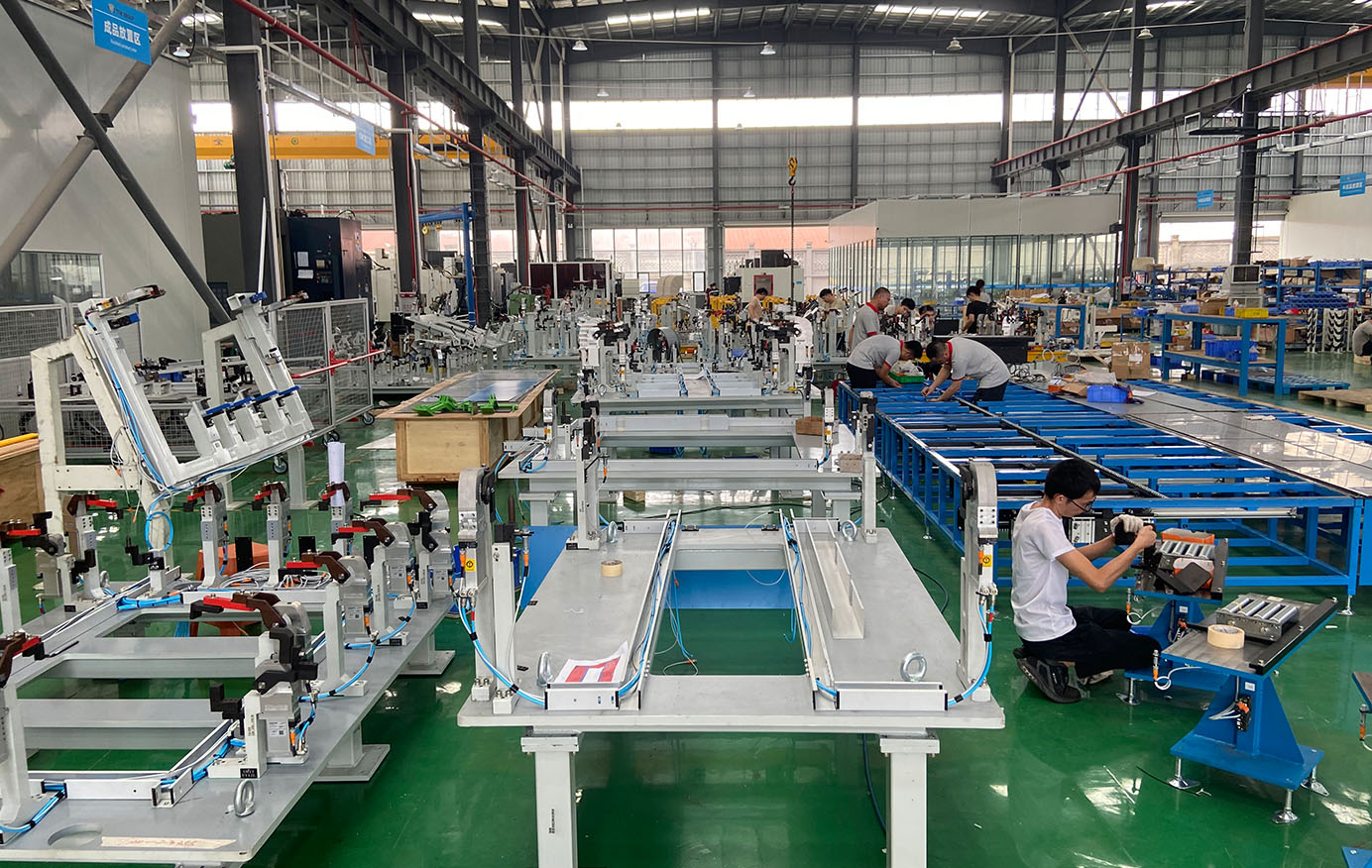

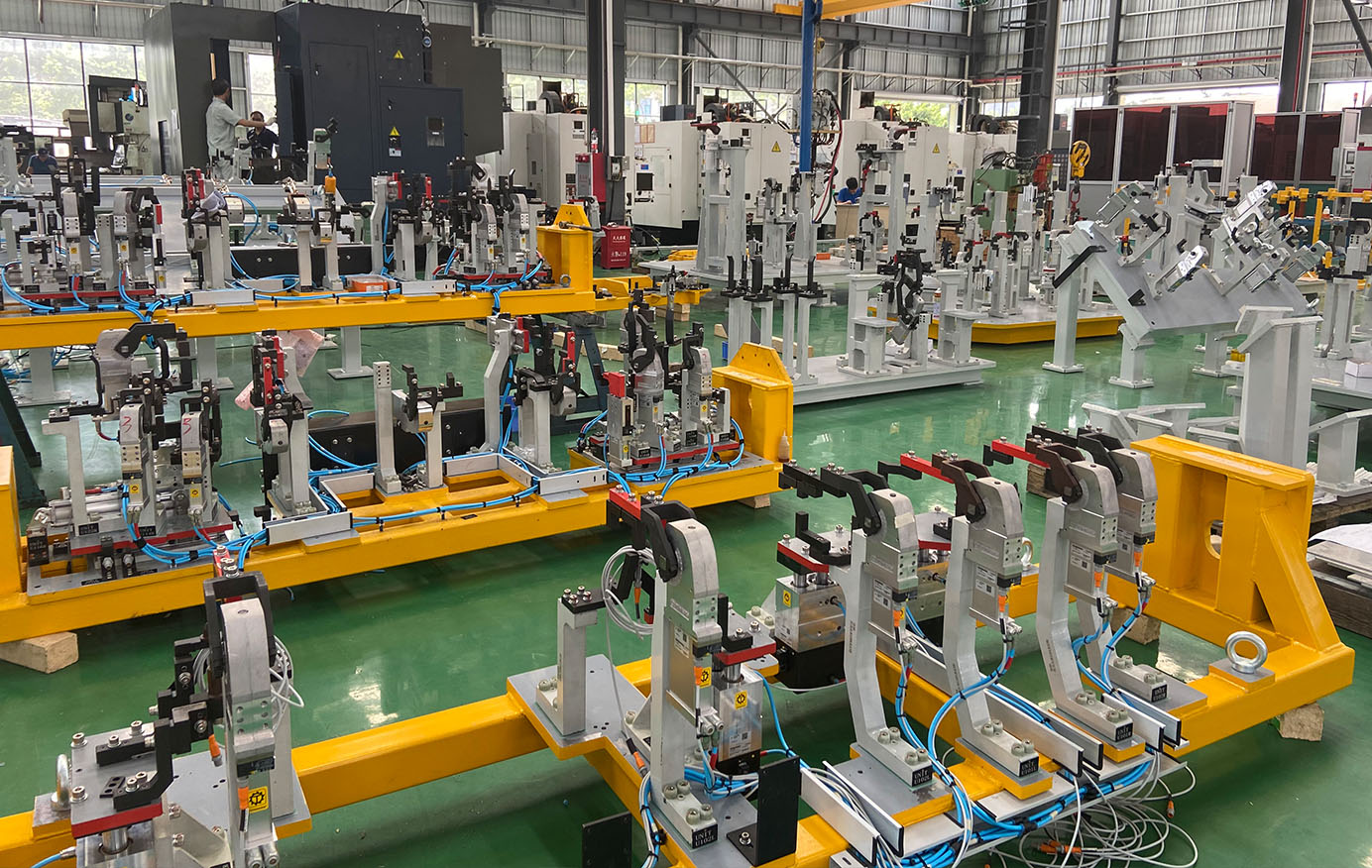
CMM Measurement Center For Hemming Dies
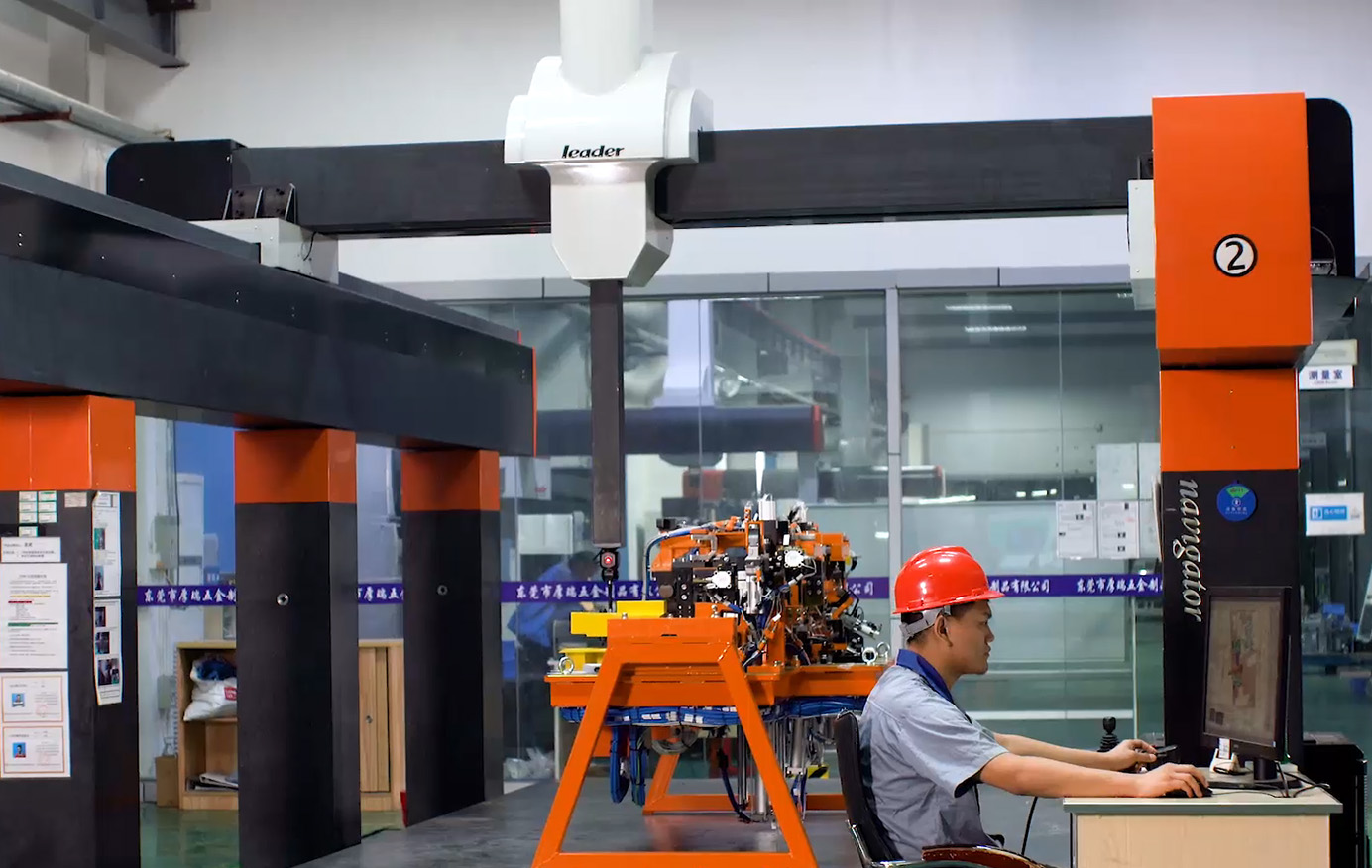
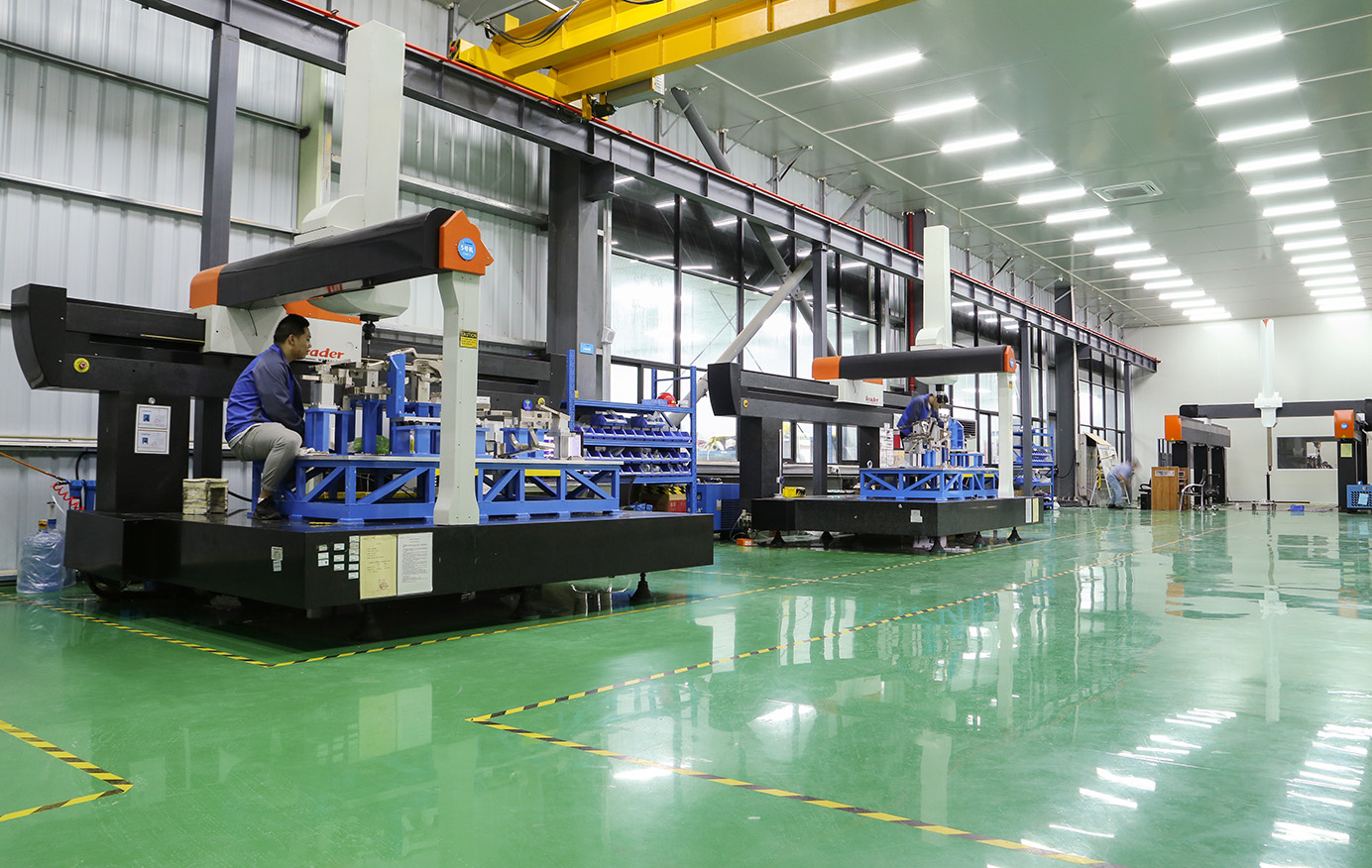
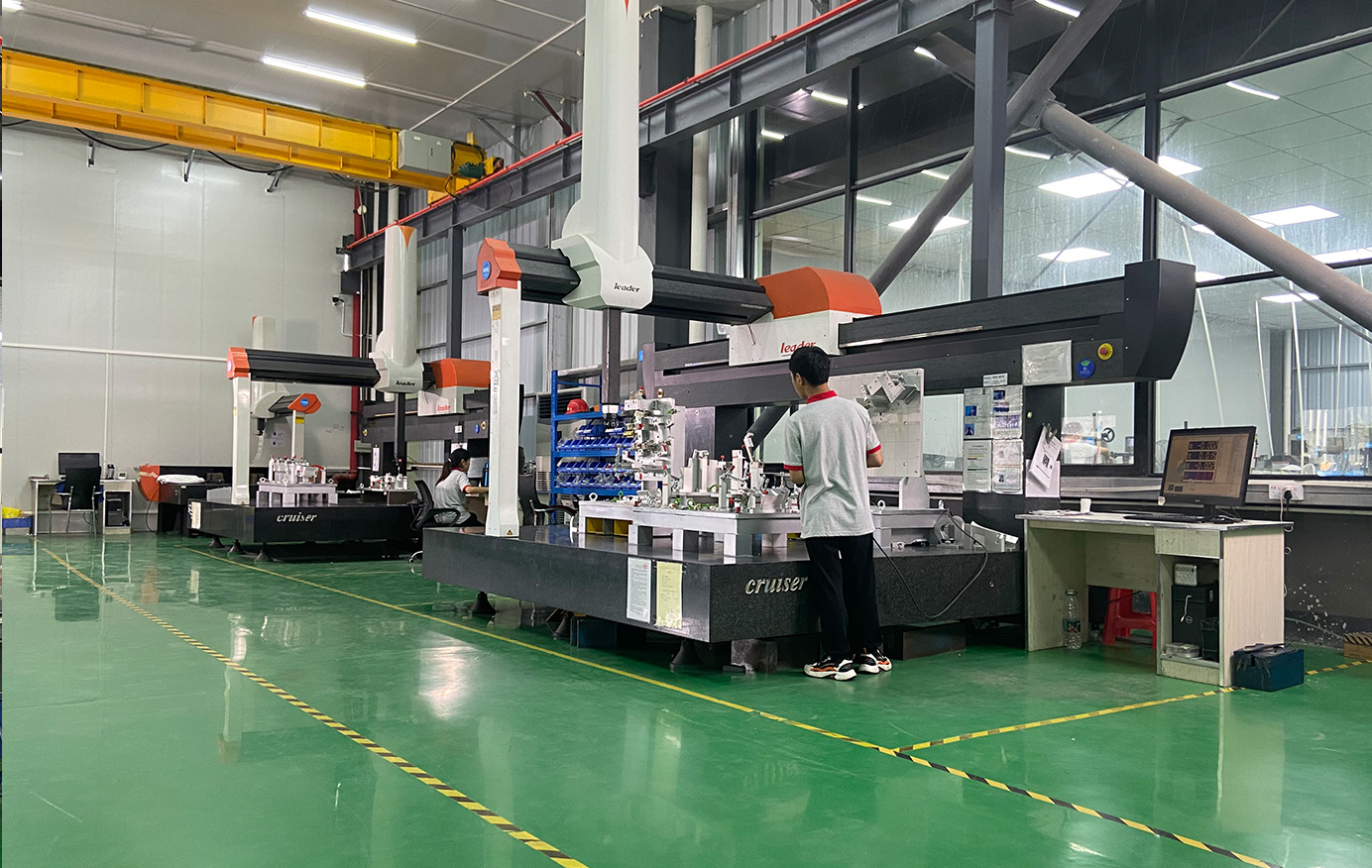
Our good trained personnel will take care every time in every program we have. We can do every requirement from the customer, to have the biggest satisfaction in the CMM as well.
3 Sets of CMM, 2 Shifts/Day(10hrs per shift Mon-Sat)
CMM, 3000*1500*1000 , Leader CMM, 1200*600*600 , Leader Blue-light Scanner
CMM, 500*500*400, Hexagon 2D Projector, Hardness Tester