Electronic checking fixture and assembly fixture for automotive manufacturing
Company Development
- In 2011, TTM was founded in ShenZhen.
- In 2012, Moving to DongGuan; Building cooperation relationship with Magna International Inc.
- In 2013 Introducing more advanced equipments.
- In 2016, Introduced large-scale CMM equipment and 5 axis CNC equipment; Cooperated with OEM Ford Completed Porsche, Lamborghini and Tesla CF projects.
- In 2017, Moving to current plant location; CNC was increased from 8 to 17 sets. Top Talent Automotive Fixtures & Jigs Co.Ltd was established
- In 2018, Cooperated with LEVDEO automotive and completed the automotion production line. 4-axis high-speed CNC was introduced, the total Qty of CNC reached 21.
- In 2019, Dongguan Hong Xing Tool & Die Manufacturer Co.,Ltd was established. (One stop service) Cooperated with Tesla Shanghai and Sodecia Germany. Built a new R&D laboratory for automation.
- In 2020, Cooperated with OEM ISUZU in SA ;Completed the RG06 One-Stop Service.
- In 2021, Moving forward with the quality belief to create a world-class enterprise.
- In 2022, TTM Group office was founded in Dongguan City, New CNC 4 axis*5 sets, New Press*630 tons, Hexagon Absolute Arm.
- In 2023, TTM is building a new factory for checking fixture and welding fixture business; adding one 2000T press.
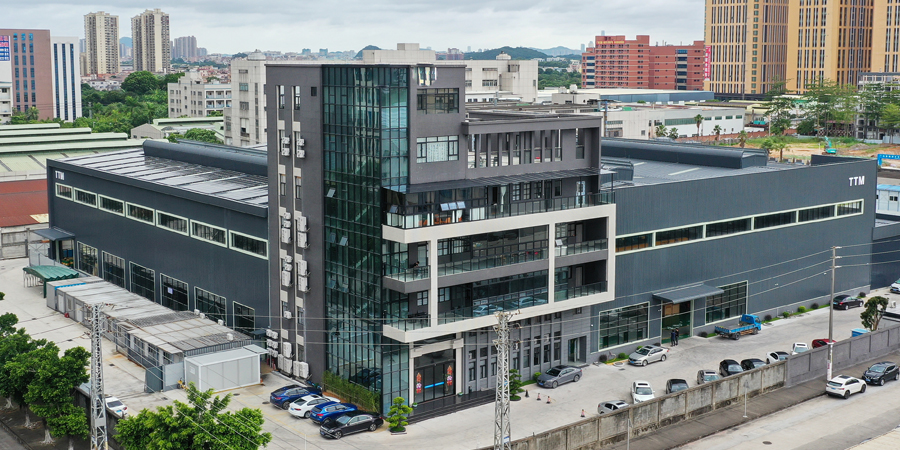
Checking Fixture & Welding Jigs Factory (Total area: 9000m² )
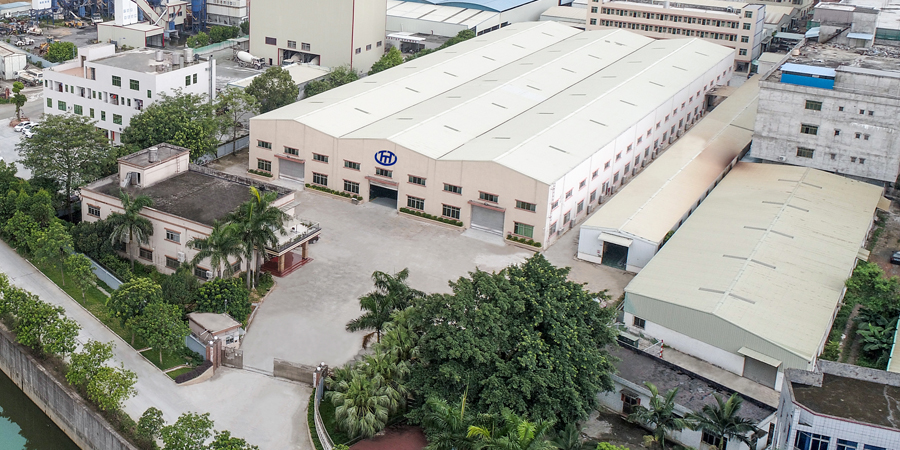
Stamping Tools & Dies and Machined Parts Factory (Total area: 16000m²)
Products Description
Product Name | Electronic Checking Fixture |
Checking fixtures Type | Single stamping checking fixtures/ assembly checking fixtures/ Holding fixtures |
Description | Single Metal Parts Checking Fixtures / Casting Aluminium Parts Checking Fixtures/ plastic checking fixtures |
Application | Automotive seat/ccb/floor etc. |
Processing Precision | +/- 0.15mm |
Accuracy for Other Profiles | Single stamping checking fixtures/ assembly checking fixtures / casting checking fixtures/ |
Accuracy for Datum Hole | +/- 0.05mm |
checking fixtures Material | Aluminum, iron, sheet, Casting iron etc. |
Design Software | Catia, Ug, CAD, STP |
3rd Party Certification | Yes |
GR&R | Yes |
Quality confirm | CMM measure,…. |
Package | Plastic or wooden box for samples, wooden plate for stamping die or as per customer's requirements |
Electronic checking fixtures play a crucial role in modern manufacturing processes, offering a range of features that contribute to increased efficiency, accuracy, and quality control. These fixtures leverage advanced electronic technologies to ensure precision in the inspection and validation of components, helping manufacturers maintain high standards in their production lines.
One key feature of electronic checking fixtures is their ability to integrate seamlessly with digital systems and computer-aided design (CAD) software. This integration allows for the creation of virtual models and simulations, enabling manufacturers to design and test their fixtures in a virtual environment before physical implementation. This not only speeds up the development process but also minimizes the risk of errors in the final fixture design. The digital compatibility of electronic checking fixtures facilitates a more agile and adaptive manufacturing environment.
Precision is a paramount requirement in manufacturing, and electronic checking fixtures excel in delivering accurate and repeatable measurements. These fixtures use advanced sensors, actuators, and measurement devices that are capable of capturing and analyzing data with high precision. The electronic components can be programmed to perform intricate measurements and inspections, ensuring that components meet specified tolerances and quality standards. This level of accuracy is essential in industries such as automotive, aerospace, and electronics, where even the slightest deviation from specifications can lead to product failures or safety issues.
Flexibility is another notable feature of electronic checking fixtures. Unlike traditional fixtures that may require manual adjustments or replacements for different components, electronic fixtures can often be reprogrammed or reconfigured to accommodate various part designs. This adaptability is particularly valuable in industries where product designs frequently change, allowing manufacturers to save time and resources by reusing existing fixtures with minimal modifications. The ability to quickly adapt to design changes enhances overall production efficiency and reduces downtime.
Real-time data feedback is a critical feature of electronic checking fixtures. These fixtures provide instant and detailed feedback on the quality of inspected components. Manufacturers can monitor and analyze this data in real-time, enabling them to identify and address issues promptly. The quick detection of defects or deviations from specifications helps prevent the production of faulty products, ultimately reducing scrap rates and improving overall yield. Additionally, the real-time data feedback allows for timely adjustments to the manufacturing process, ensuring continuous improvement and optimization.
Integration with Industry 4.0 principles is becoming increasingly prevalent in manufacturing, and electronic checking fixtures align with this trend. These fixtures can be connected to the Internet of Things (IoT) and other smart manufacturing technologies, enabling remote monitoring and control. Manufacturers can access fixture data, monitor performance, and even make adjustments from remote locations. This connectivity enhances overall efficiency, facilitates predictive maintenance, and supports the implementation of data-driven decision-making processes.
In conclusion, electronic checking fixtures represent a significant advancement in manufacturing technology, offering a combination of precision, flexibility, real-time feedback, and digital integration. As industries continue to evolve towards smart manufacturing and Industry 4.0, the role of electronic checking fixtures is expected to become even more prominent in ensuring the quality and efficiency of production processes.
Solutions (checking fixture)
Electronic Checking Fixture
Single Sheet Metal Checking Fixtures
Single Plastic Component Checking Fixtures
Single Carbon Fibre Checking Fixtures
Assembly Sheet Metal Checking Fixtures
Assembly Plastic Component Checking Fixtures
Assembly Carbon Fibre Checking Fixture
Hot Forming Checking Fixtures
C.M.M. holding fixtures
Body-in-White Checking Fixtures
Cubing Checking Fixtures
Automotive Lamp Checking Fixture
Automotive Glass Checking Fixture
ISO Management System For Checking Fixture
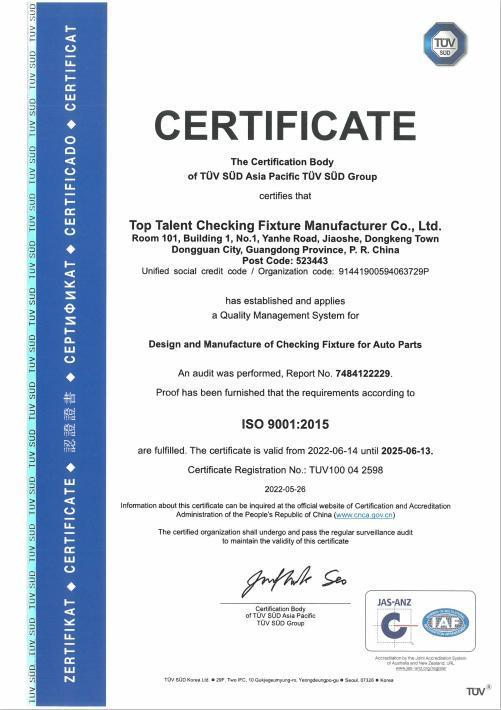
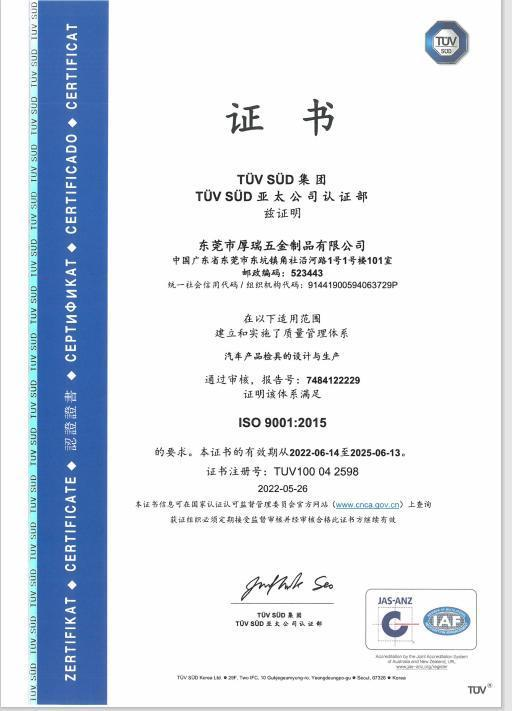
Our Checking Fixture Team
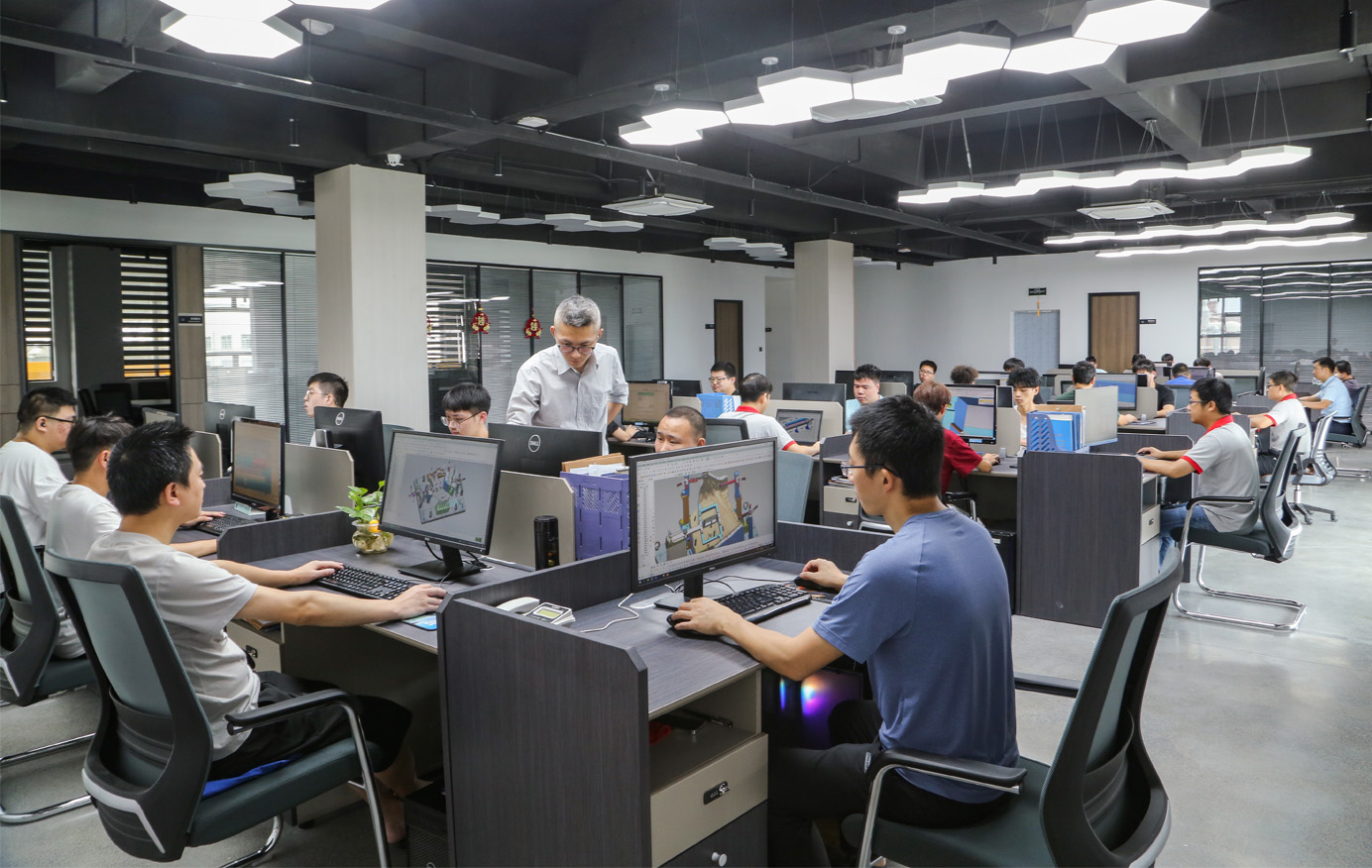
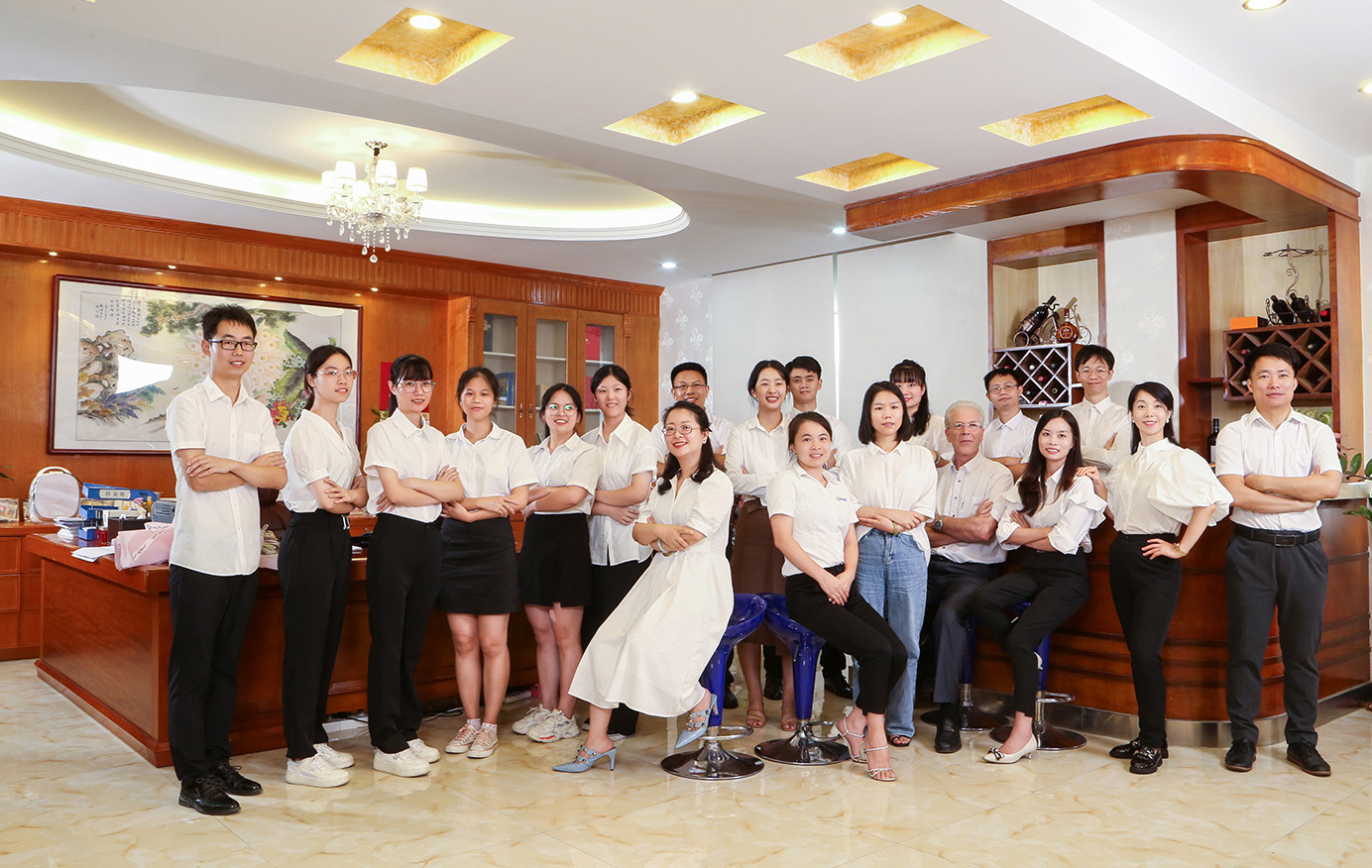
Our Manufacture Checking Fixtures Advantages
1.Rich experience in automatic manufacturing and enterprise management.
2.One Stop Service for stamping die, checking fixture, welding fixtures and cells to achieve timing and cost saving, communication convenience, to maximize customer profits.
3.Professional engineering team to finalize the GD&T between single part and assembly component.
4.Turnkey Solution Service-Stamping Tool, Checking Fixture, Welding Fixtures and Cells with one team.
5.Strong capability with international technical support and partnership cooperation.
6.Big capacity: Checking Fixture, 1500 sets/year;Welding Fixture and Cells, 400-600 sets/year; Stamping Tools, 200-300 sets/year.
Major Projects Experience Of Checking Fixture
Reference Project Completed in 2022 | |||||||
GM | GM CCB's(17126&27&28) | C223-L232 | GM D2UX-2 | P002297 | BT1CC | ||
GM | 31XX2-MY2024 | ELVC | BEV3 | ||||
Volvo | SPA2 | P61A | P61A-CHS45 | EXT019 | INT26S | ||
VW | KKF | VW336 | VW 316 A-SUV | ||||
Ford | Ford Refurbishment | P703-22B | FORD V769 | P703 PHEV | |||
GS | V769 | X52 | 5ECHO | ||||
BMW | G6X | G45 | F65 | G48 | |||
Nissan | P13C | P42S | H61P | ||||
Polestar | P61A | P611 | |||||
FCA | V900 | V800 | |||||
Rivian | #1209032 | #1209033 | |||||
BYD | HCEEC Seat ASSY | ||||||
Mazda | KJ380 | ||||||
Honda | S233 | ||||||
FormService | KAMAZ K5 | ||||||
PWO | DAIMLER | ||||||
Tesla | Tesla Everest model | ||||||
Mercedes | MMA | ||||||
Audi | AUDI NF AU436 SB | ||||||
Reference Project Completed in 2021 | |||||||
GM | BT1CX | BEV3 BIW | BT1UG | C234 | BEV3/C234 | C1YC-2 | |
GM | Presstran GM eLCV | BV1Hx-Elcv | T31XX | A100 | BT1CC | BT1 XX | |
BMW | BMW Mini F66 TSV | G05&G06 | BMW 25967 | F6X | BMW F95-F96 | BMW Mini U25 Countryman TSV | G09 |
Ford | Ford S650 Group #2 | MY 2022 | Ford C234 | Ford P703 | Ford U725 | ||
Ford | Ford_P703N_ECN371 | J73 | P703N | P708 | |||
Daimler | Daimler 223 | Daimler 206 | X294 | ||||
Volvo | Volvo V536 | Volvo CX90 | 723K | ||||
Toyota | Toyota 135D | Toyota 24PL | |||||
LADA | LADA BJO Addons | LADA Granta | |||||
Rivian | RPV | PRV-700 | |||||
Honda | Honda-ILX | T90 | |||||
YANFENG | M189 | ||||||
Isuzu | VF87 | ||||||
Mercedes-Benz | V214 | ||||||
NISSAN | P13C | ||||||
FCA | FCA 516 | ||||||
Skoda | SK351 Rapid PA3 | ||||||
Honda | 23M CR-V CCB | ||||||
Tesla | Model Y | ||||||
Reference Project Completed in 2020 | |||||||
Daimler | Mercedes X294 | Mercedes X296 | V295 WCC (China) | V295 WD | V206 and EVA2(206BT) | V254 | |
Ford | P703 | Carry-over | U725 | BX755 | P703 & J73 | P758 | |
BMW | G87 | BMW PASSD | G07 | G09 | |||
GM | BT1FG | 31XX-2 | BT1XX | C1YX | |||
TOYOTA | 340B RAV4 | 780B | 817B | 922B | |||
VW | VW316 | MEB 316 | SK 351/3 RU PA2 | ||||
Honda | 2GT | 4DTG | |||||
Tesla | Model Y | Tesla Rear Side | |||||
Volvo | P519 | ||||||
Porsche | Macan II PO426 S | ||||||
Linecross | BY636 EWB | ||||||
Renault | ADP Project | ||||||
Mazda | Mazda J34A |
Checking Fixture Manufacturing Center
We can build all kinds of different size welding fixture including large size as we have big CNC Machines. With a variety of mechanical equipment such as milling, grinding, wire cutting machines and drilling machines, we can effectively and accurately control the processing process.
25 sets of CNC with 2 shift running
1 Set of 3-Axis CNC 3000*2000*1500
1 Set of 3-Axis CNC 3000*2300*900
1 Set of 3-Axis CNC 4000*2400*900
1 Set of 3-Axis CNC 4000*2400*1000
1 Set of 3-Axis CNC 6000*3000*1200
4 Set of 3-Axis CNC 800*500*530
9 Set of 3-Axis CNC 900*600*600
5 Set of 3-Axis CNC 1100*800*500
1 Set of 3-Axis CNC 1300*700*650
1 Set of 3-Axis CNC 2500*1100*800
We have more than 352 employees, 80% of which are senior technical engineers. Tooling division: 130 employees, Welding fixture division:60 employees, Checking fixture division:162 employees, We have a professional sales & project management team, long-term service overseas projects, from RFQ to production, shipment, after-sales, our team can handle all problems for our customers in Chinese, English and German Language.
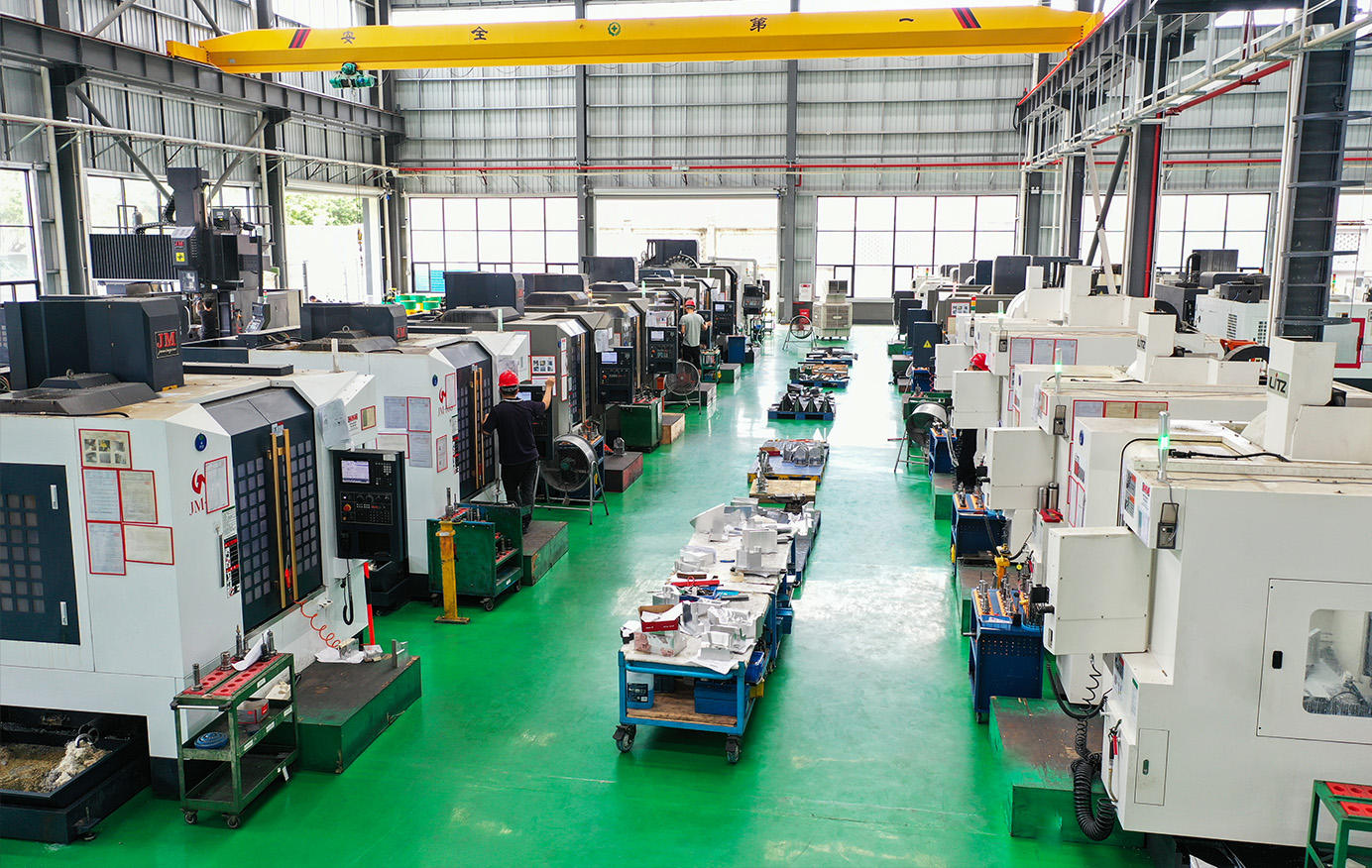

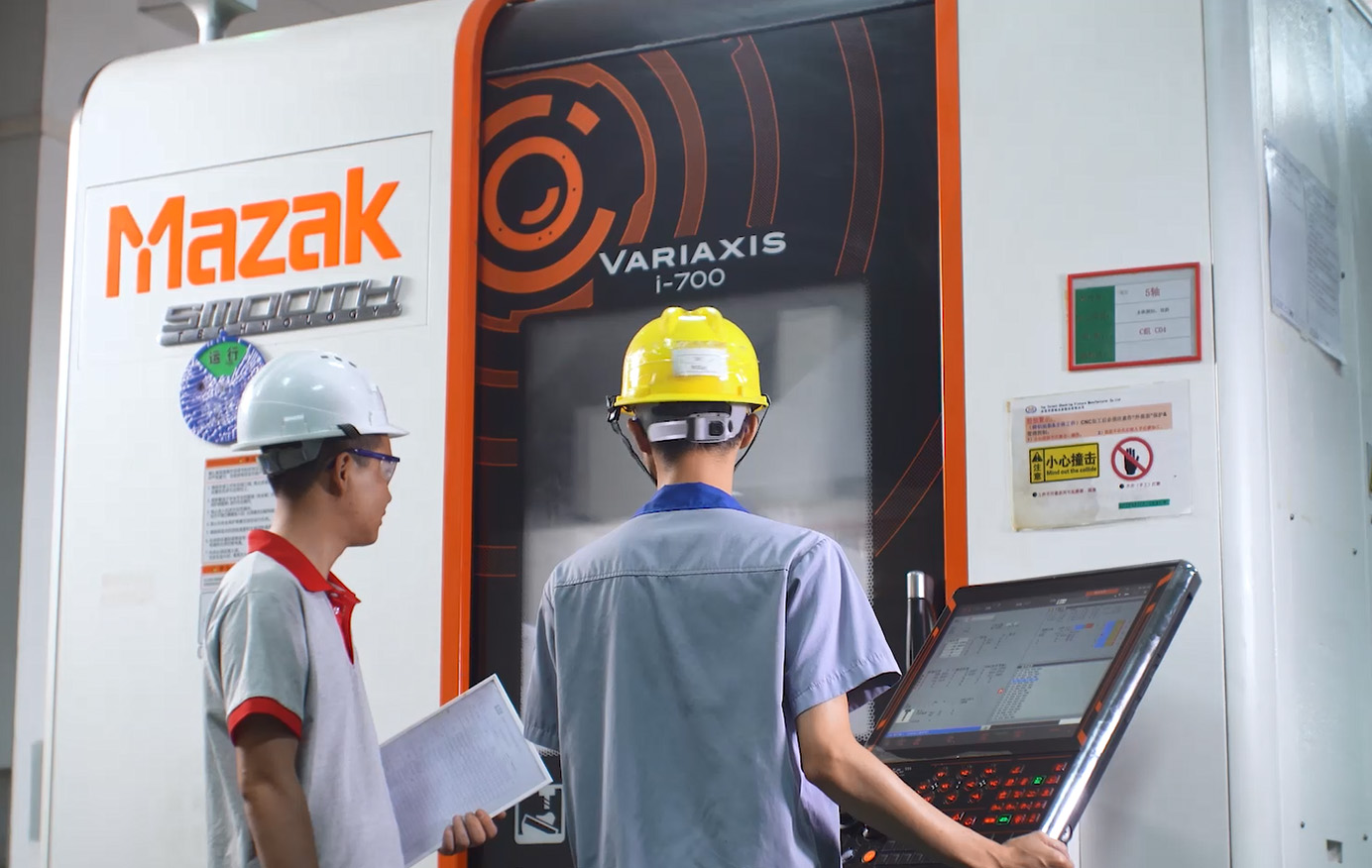
5 Axis CNC -Machine
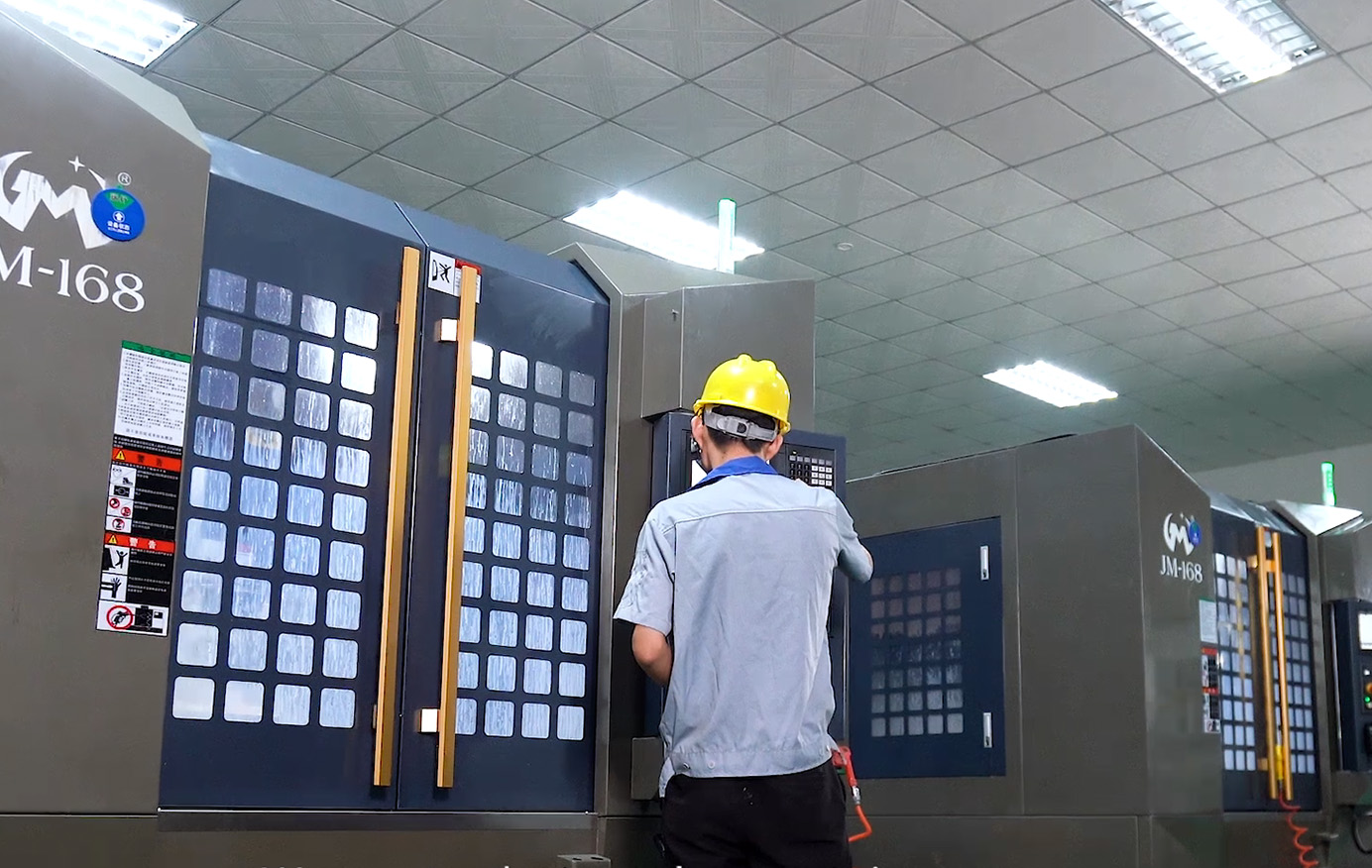
4 Axis CNC -Machine
Checking Fixture Assembly Center
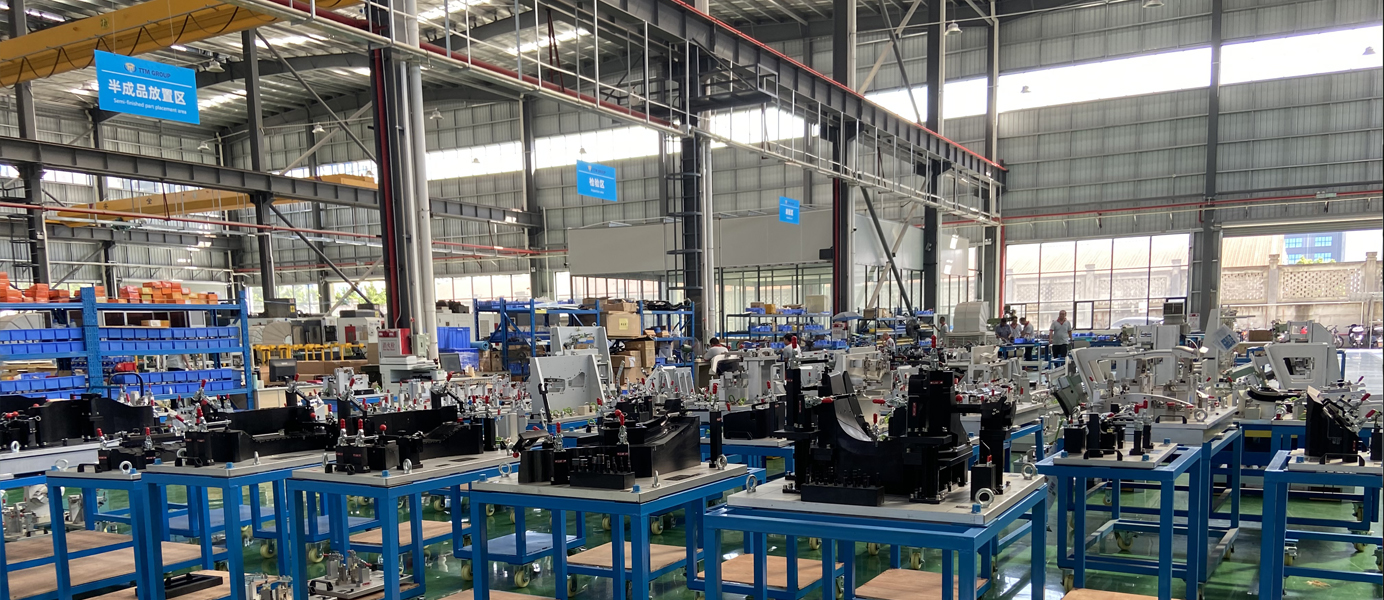
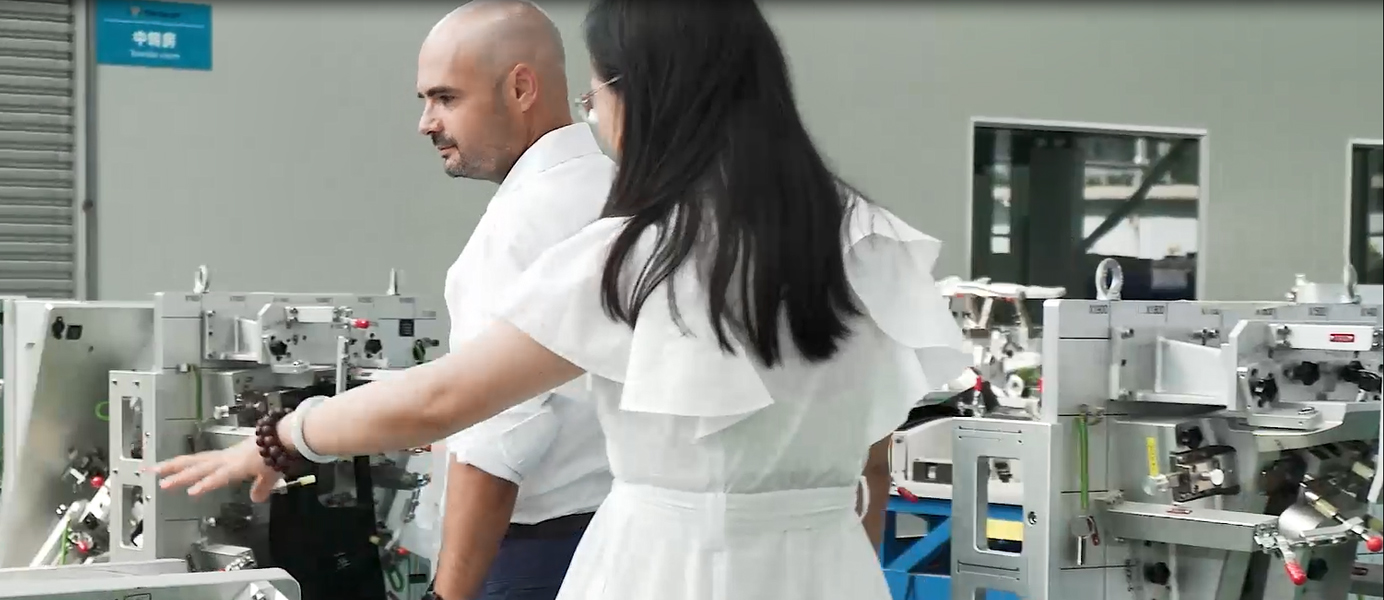
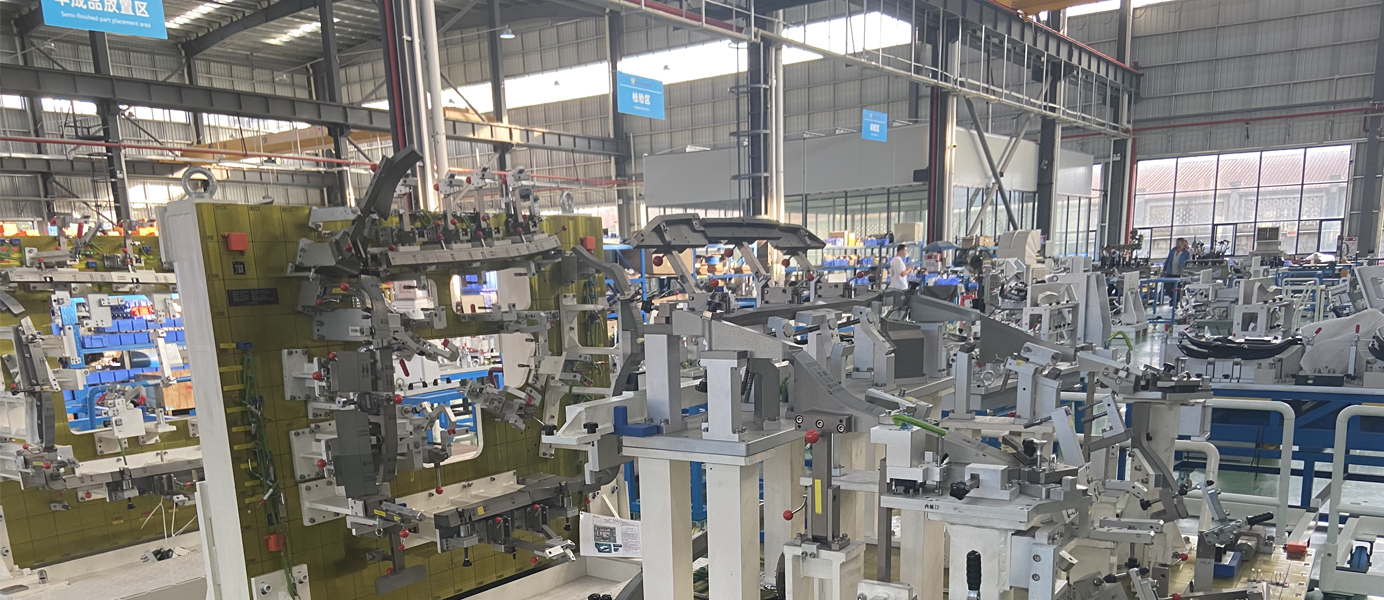
CMM Measurement Center For Checking Fixture
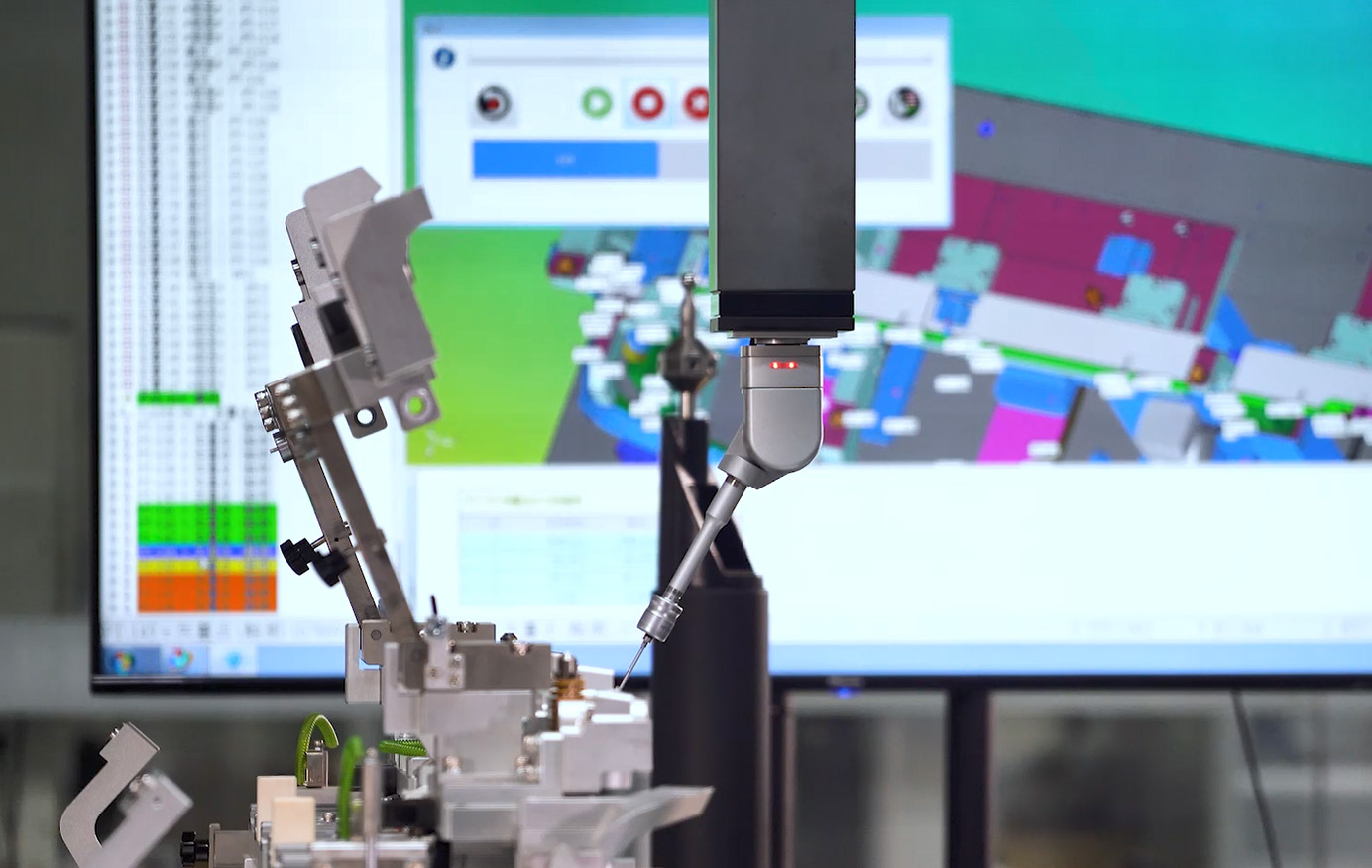
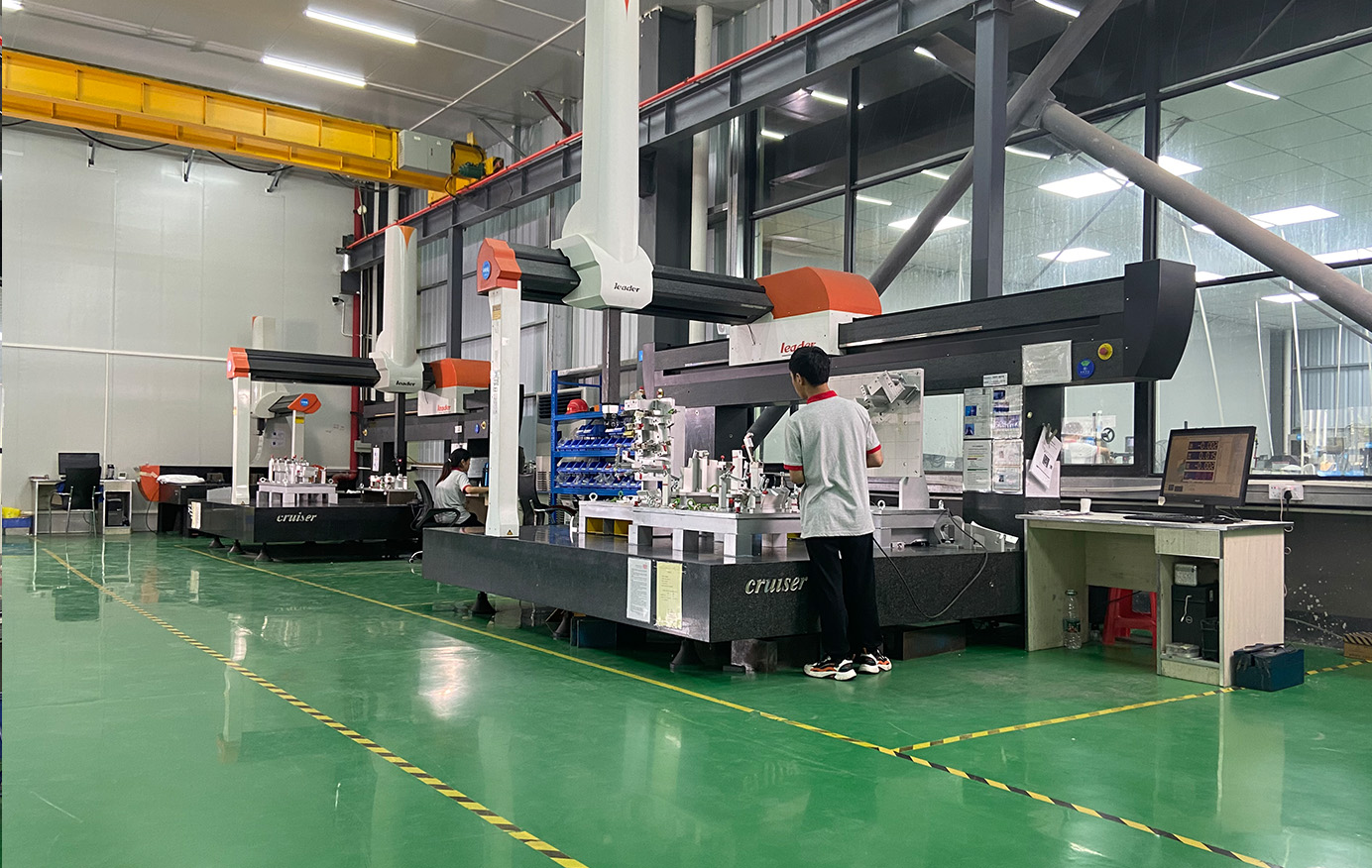
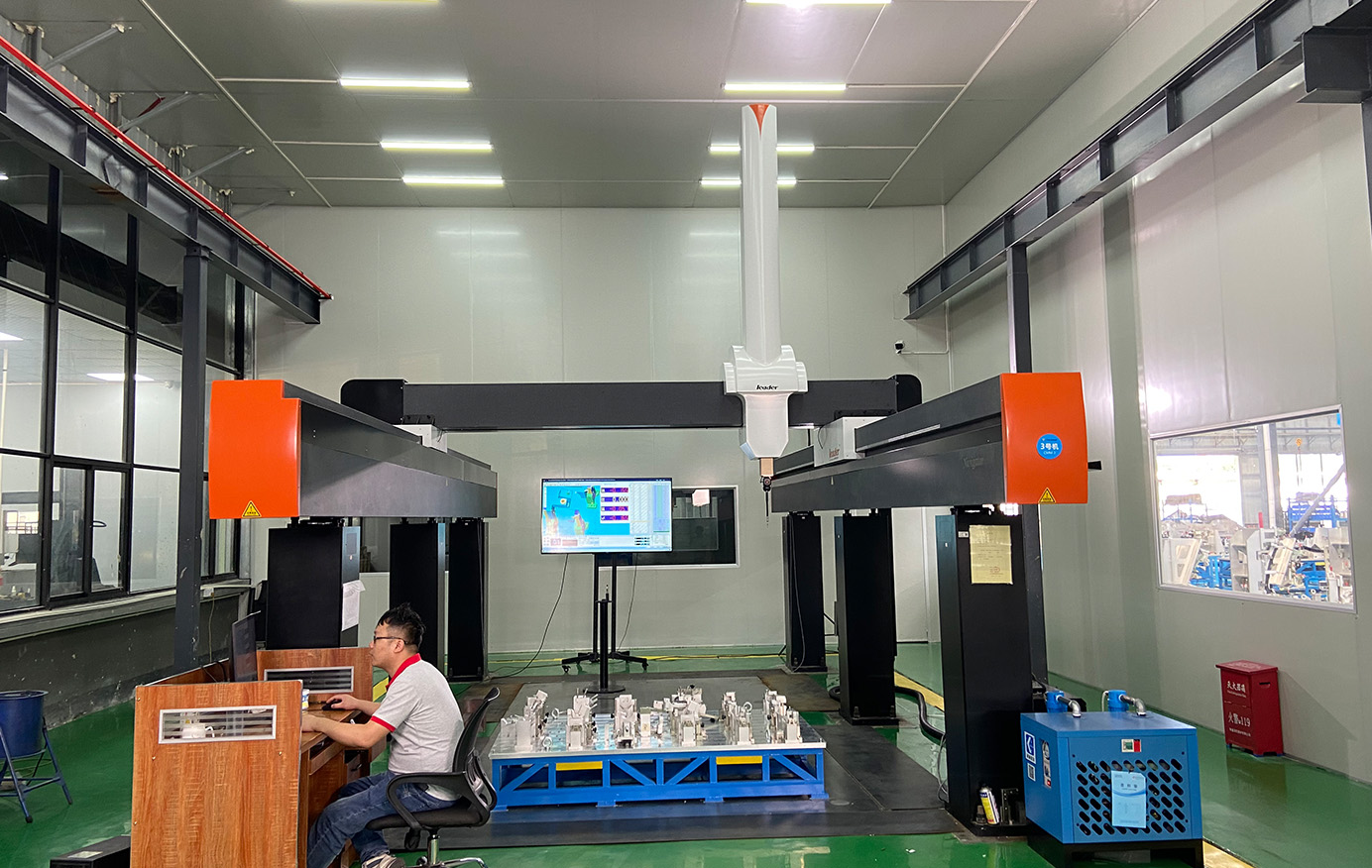
Our good trained personnel will take care every time in every program we have. We can do every requirement from the customer, to have the biggest satisfaction in the CMM as well.
3 Sets of CMM, 2 Shifts/Day(10hrs per shift Mon-Sat)
CMM, 3000*1500*1000 , Leader CMM, 1200*600*600 , Leader Blue-light Scanner
CMM, 500*500*400, Hexagon 2D Projector, Hardness Tester
CMM Inspect Report of Electronic Checking Fixtures
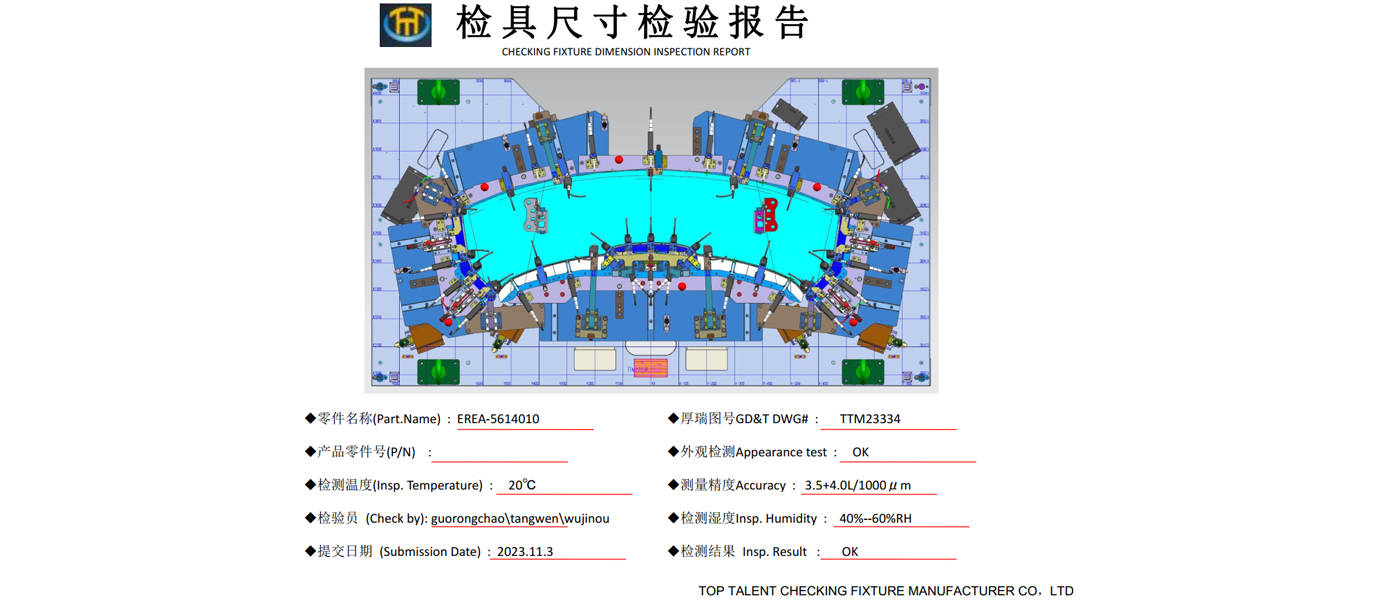
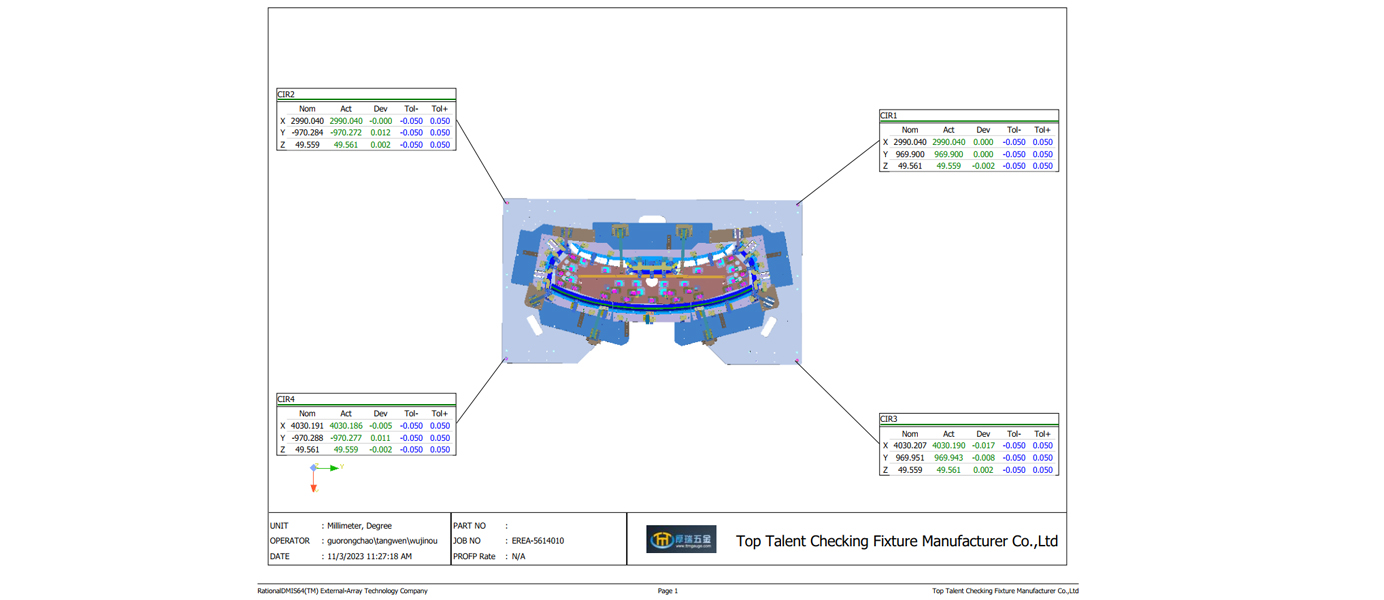